Energy & Cost Impacts: High Efficiency Motors
The United States Department of Energy (DOE) as well as the California Energy Commission (CEC) specify minimum motor efficiency requirements and, depending on the application, the ability to modulate the speed of the motor. These stipulations were put in to place mainly to reduce greenhouse gas emissions and make the electrical grid more reliable. For the end users, this also results in significant energy and cost savings.
When many people consider the cost of a motor, they only look at the price tag. While this is a significant portion of the overall cost it does not tell the entire story. When considering the cost of a motor, three things should be accounted for:
- Purchase Cost
Many premium efficiency motors have a purchasing cost that is higher than standard efficiency motors. This is because the efficient motors have a newer design, often with more costly materials. Internal components of highly efficient motors are also held to higher standards and may have a more thorough quality assurance process at the factory. As the premium efficiency motors have more time in the market the higher cost is likely to decrease. - Operational Cost
This is directly related to the energy saved from improved motor efficiency. Often the cost of the energy saved can pay for the higher purchased price quickly. The US Department of Energy has developed a simple way to estimate the annual dollar savings when using an efficient motor:
For example, if we consider a 7.5 HP motor running at 80% of load for 8000 hours a year with an average energy cost of $0.13 $/kWh and a premium efficiency motor has an efficiency of 80% as opposed to 78%; that would save $149.20 a year. The simple payback in years can be calculated by dividing the premium price (price of premium motor that is greater than the standard motor) by the annual dollar savings. Continuing with example, if the premium efficient motor cost about $450 more than the standard motor the simple payback would be 3 years.For more savings information, a detailed simulation of motor use was performed using the Department of Energy’s (DoE) EnergyPlus software. This model using the DoE’s stand-alone retail standard reference building, which is representative of a commercial building that has four roof-top units (RTUs) to provide heating and cooling. The results for each motor can be found on their respective product page.
- Maintenance and Replacement Cost
Most premium efficiency motors have a longer life and require less maintenance than standard efficiency motors. This should be accounted for when considering the overall cost of using a motor for a specific application. Again, as stated above, the long-term cost savings of choosing a motor of this type is not often incentivized in the upfront purchasing phase of the project.
The energy savings numbers provided in the plots below are illustrative and based on ranges of building vintages for each commercial building type. There are two sets of plots. The first is the fan energy savings. This represents the energy savings in the motor alone when replacing a classic induction fan motor with the high efficiency motors tested. The second plot is the energy savings of the entire building system that be achieved by replacing those same fan motors. In any actual building, energy savings will differ based on the specifics of the building, orientation, envelope, building systems, and occupancy.
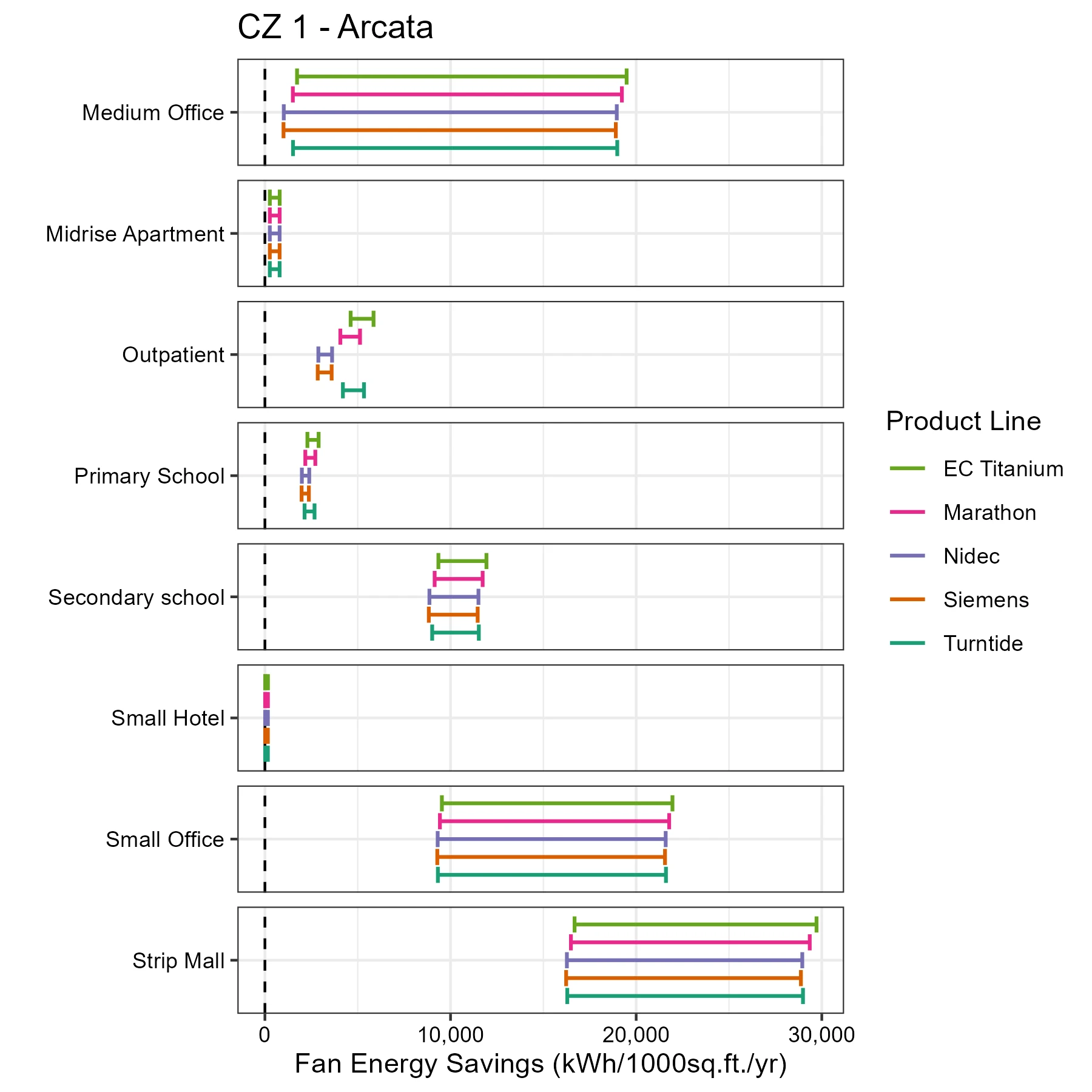
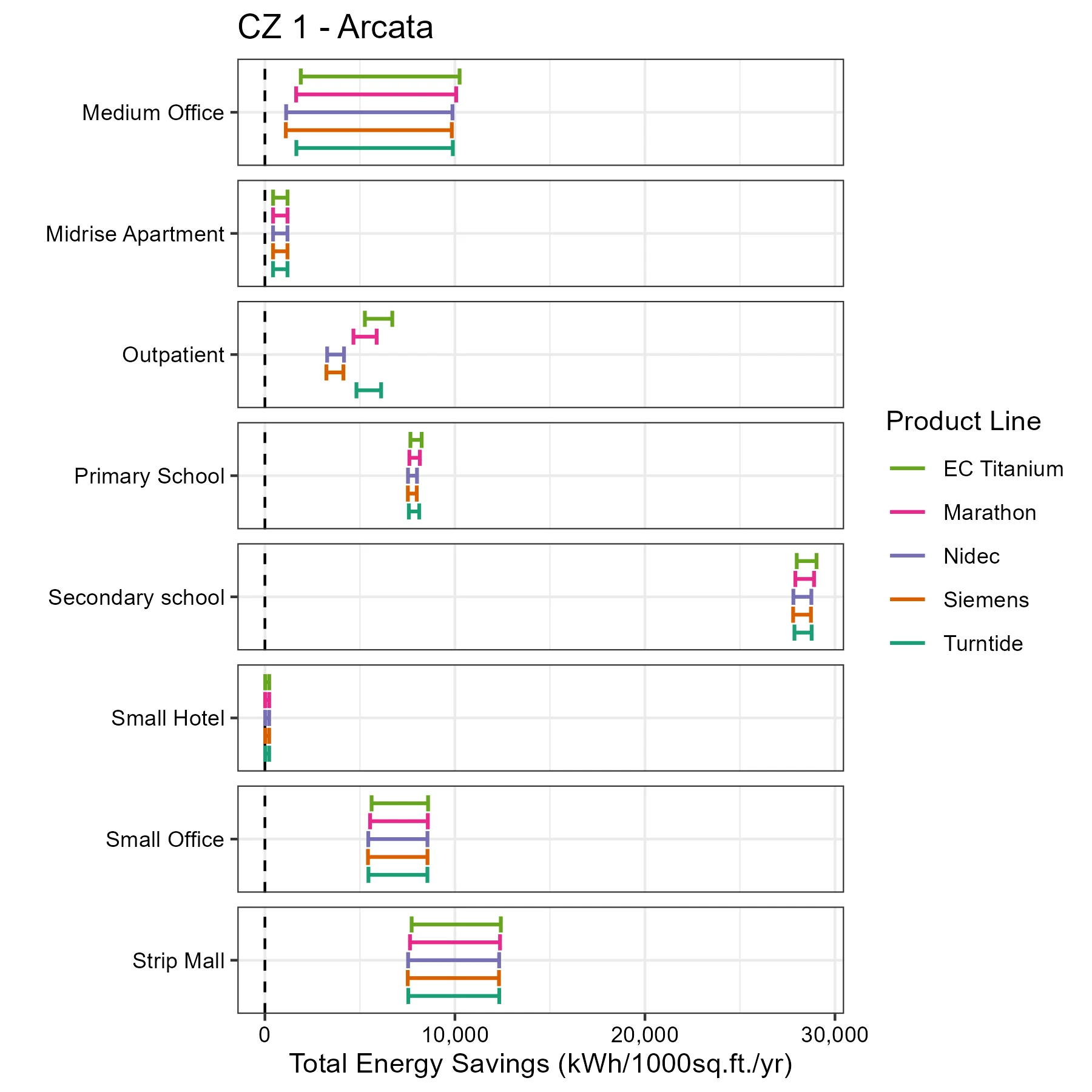
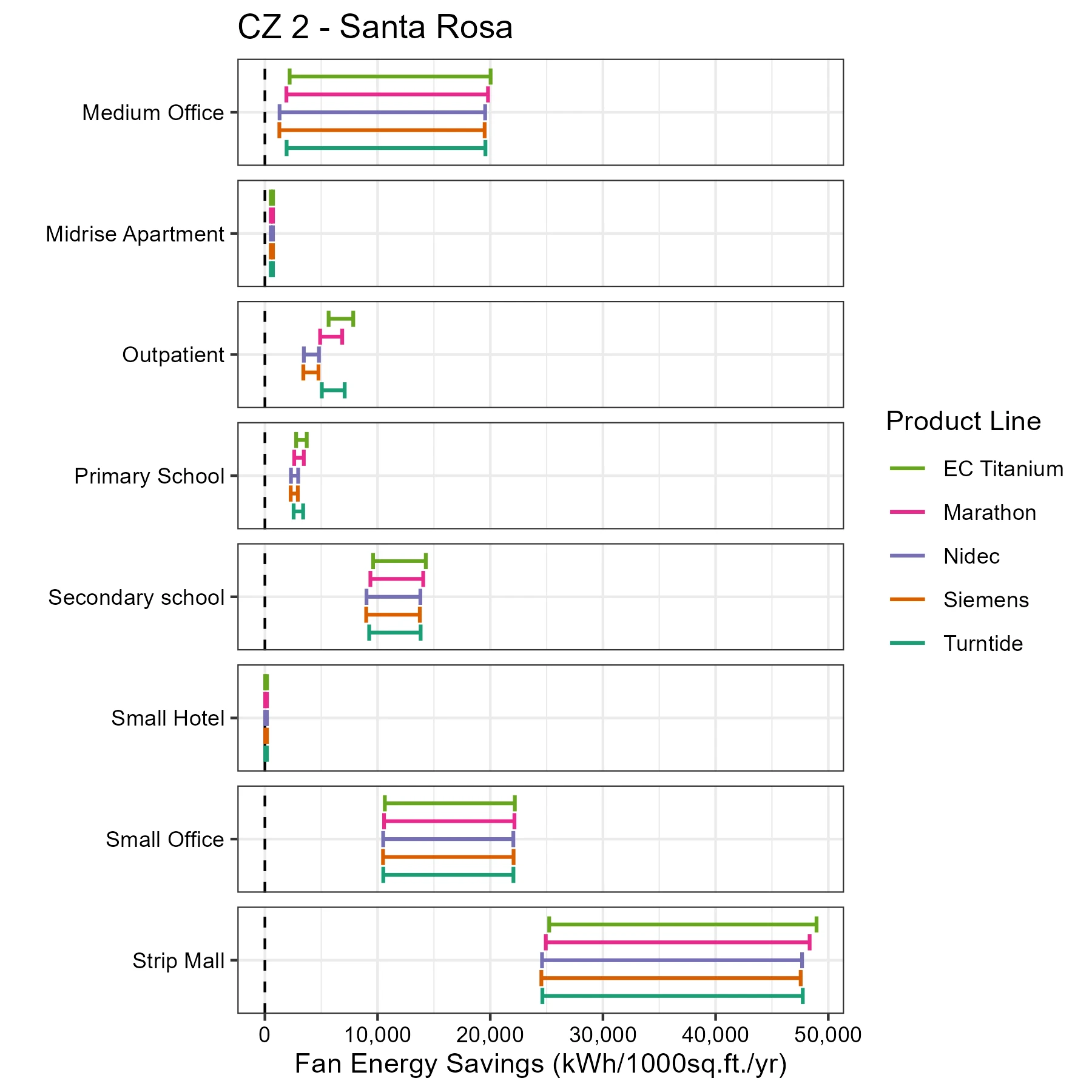
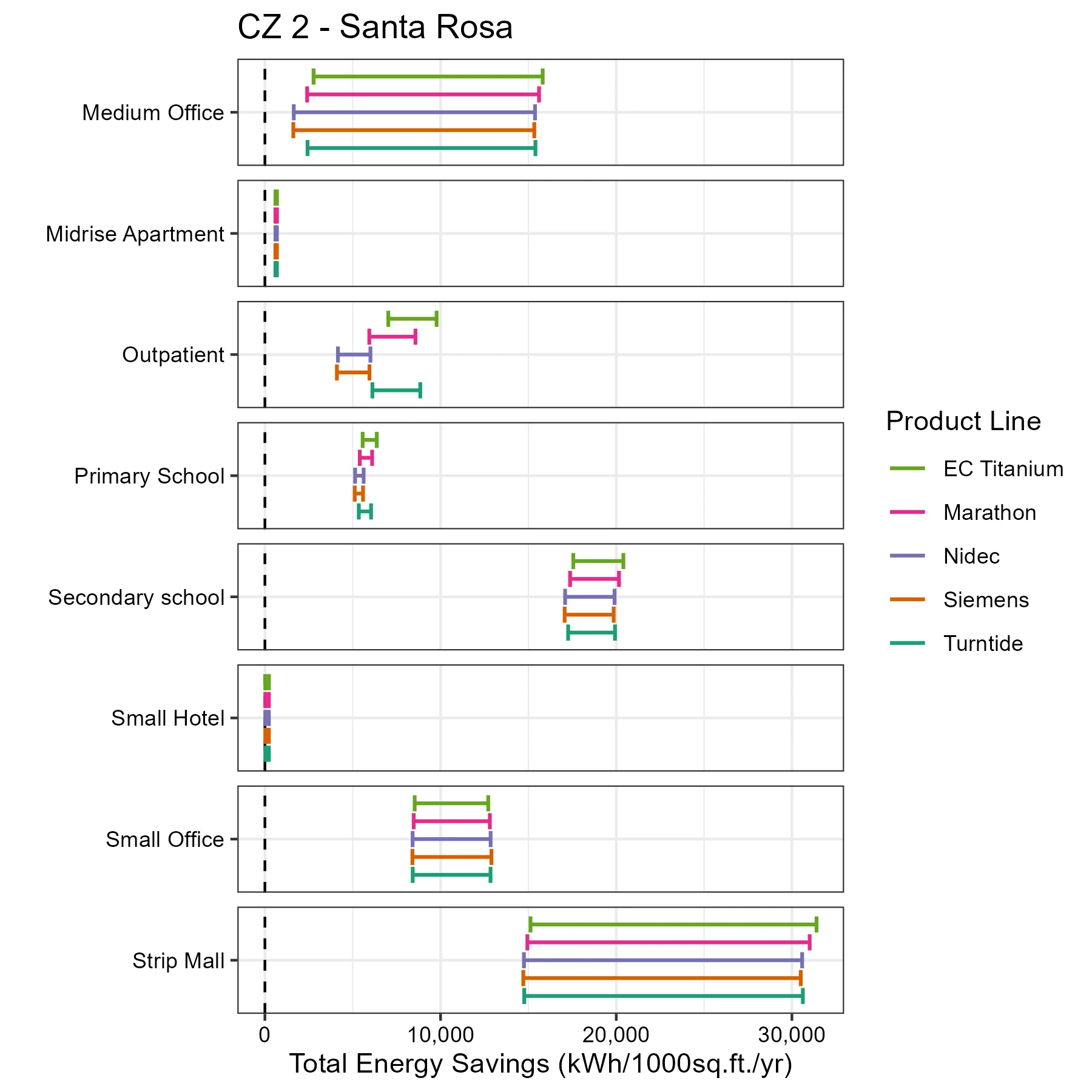
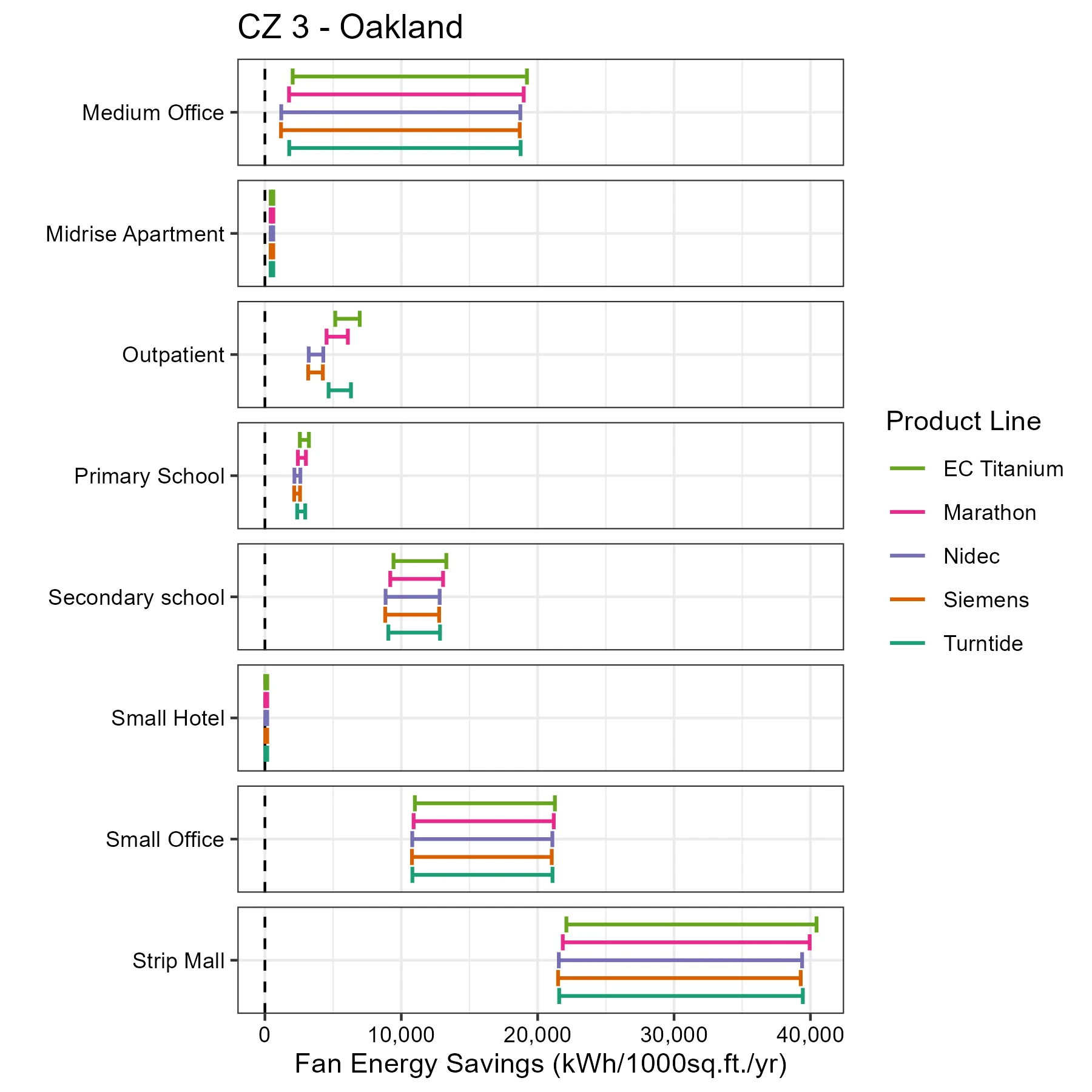
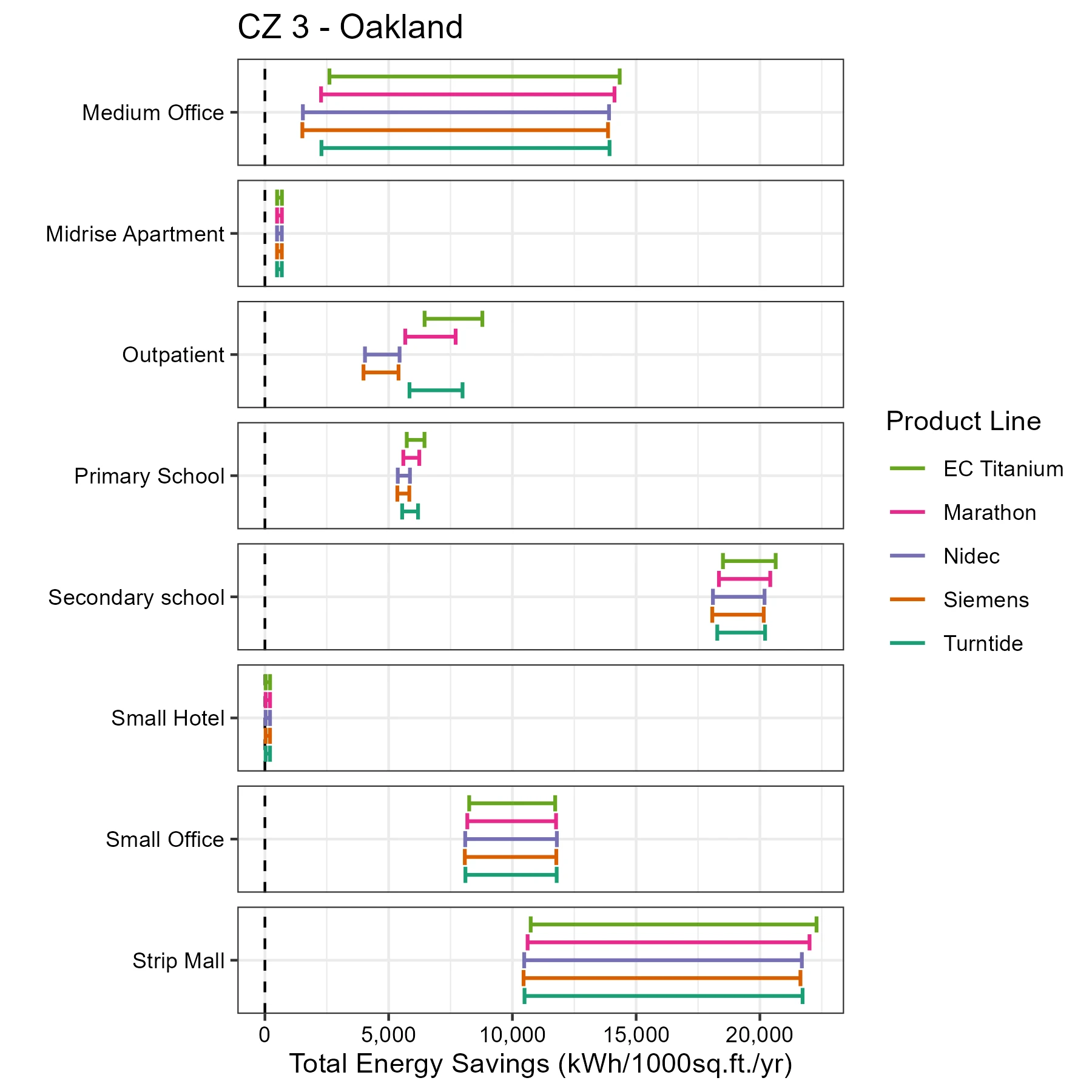
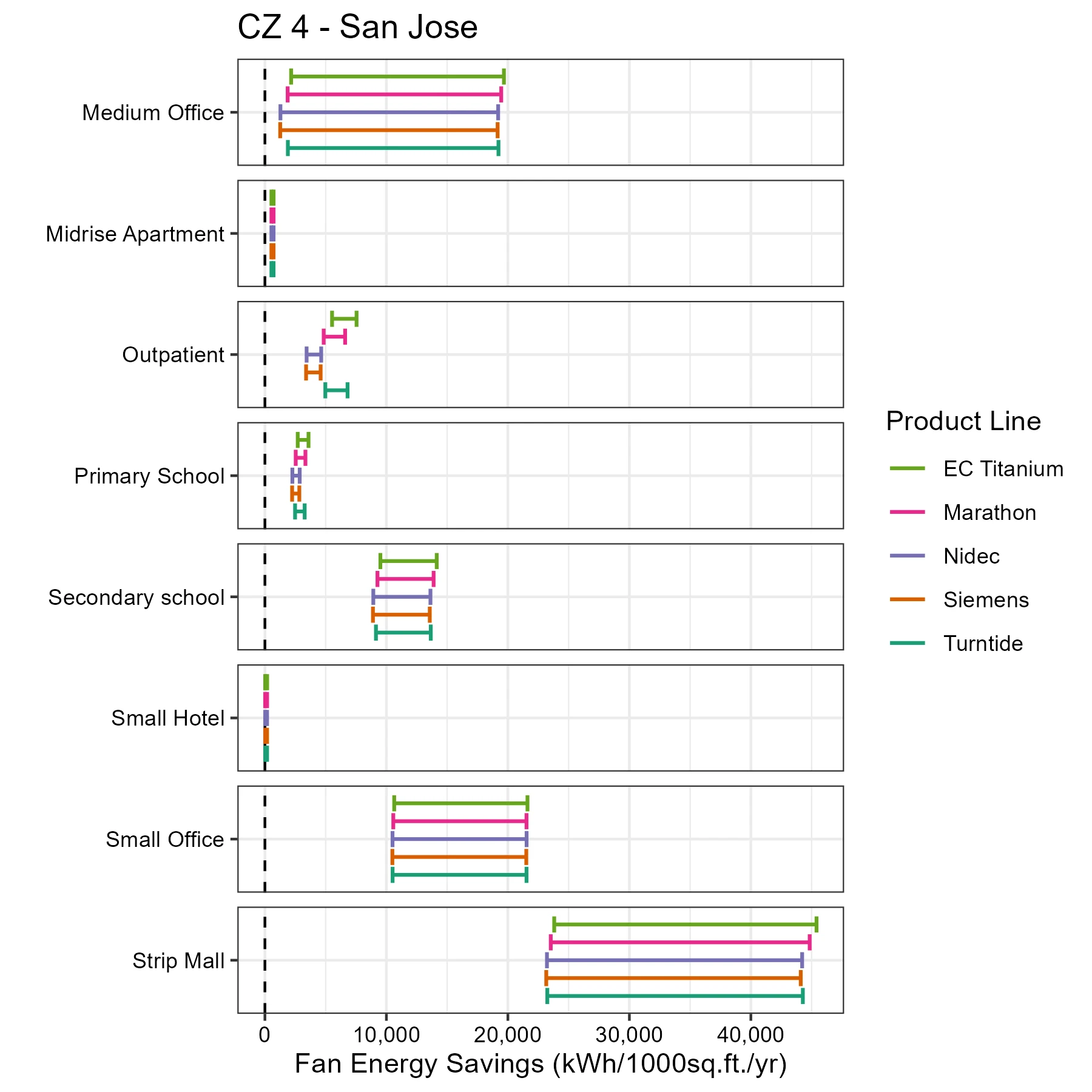
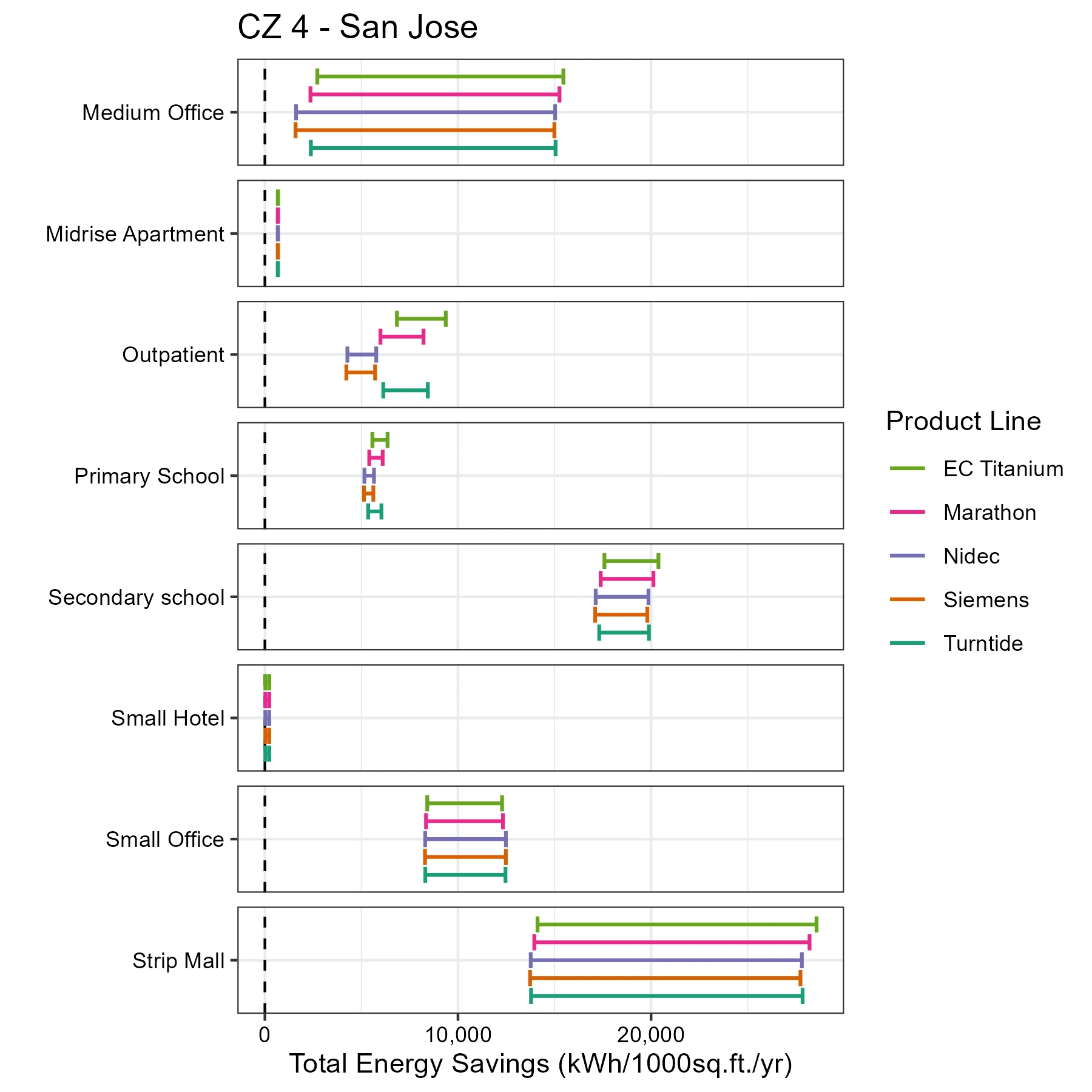
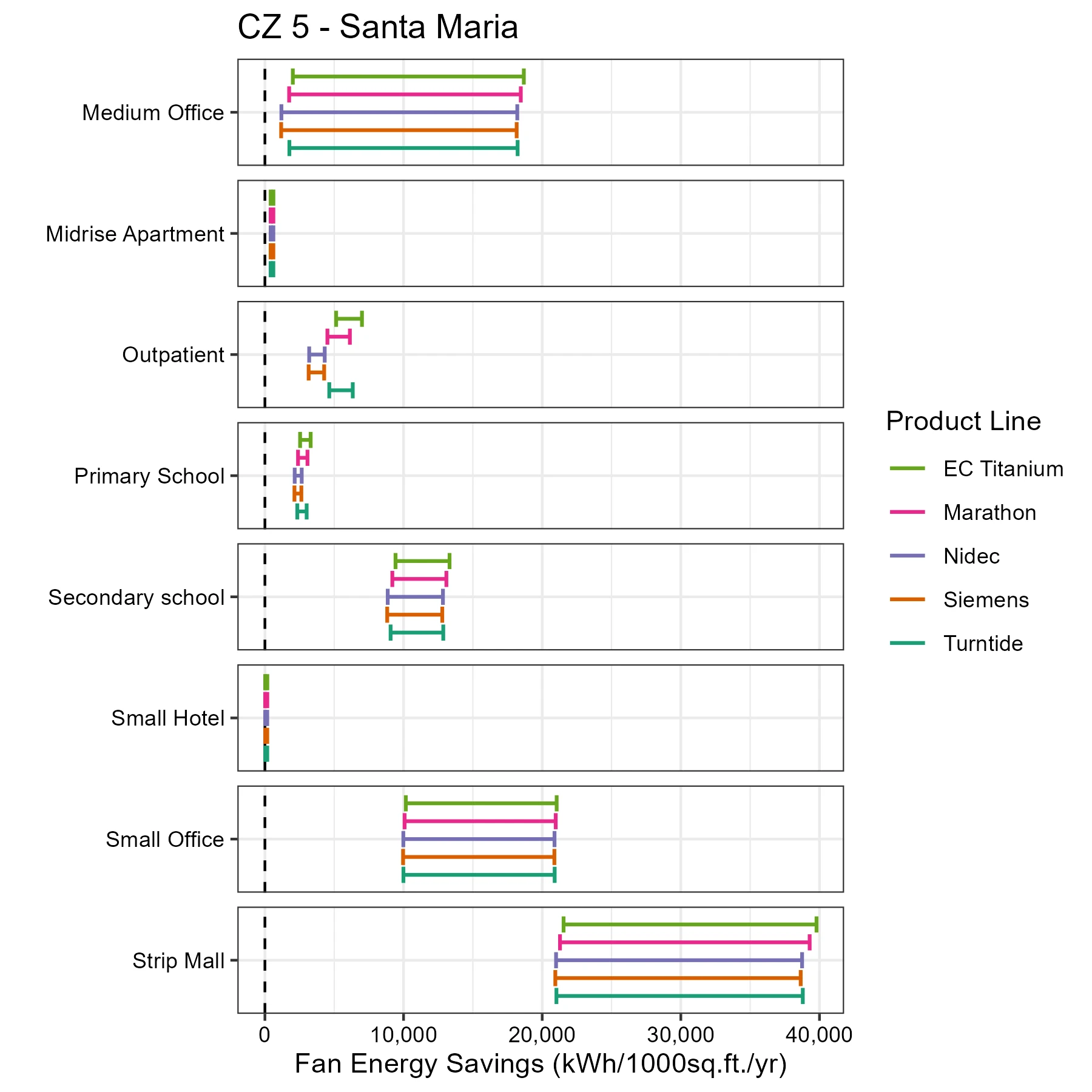
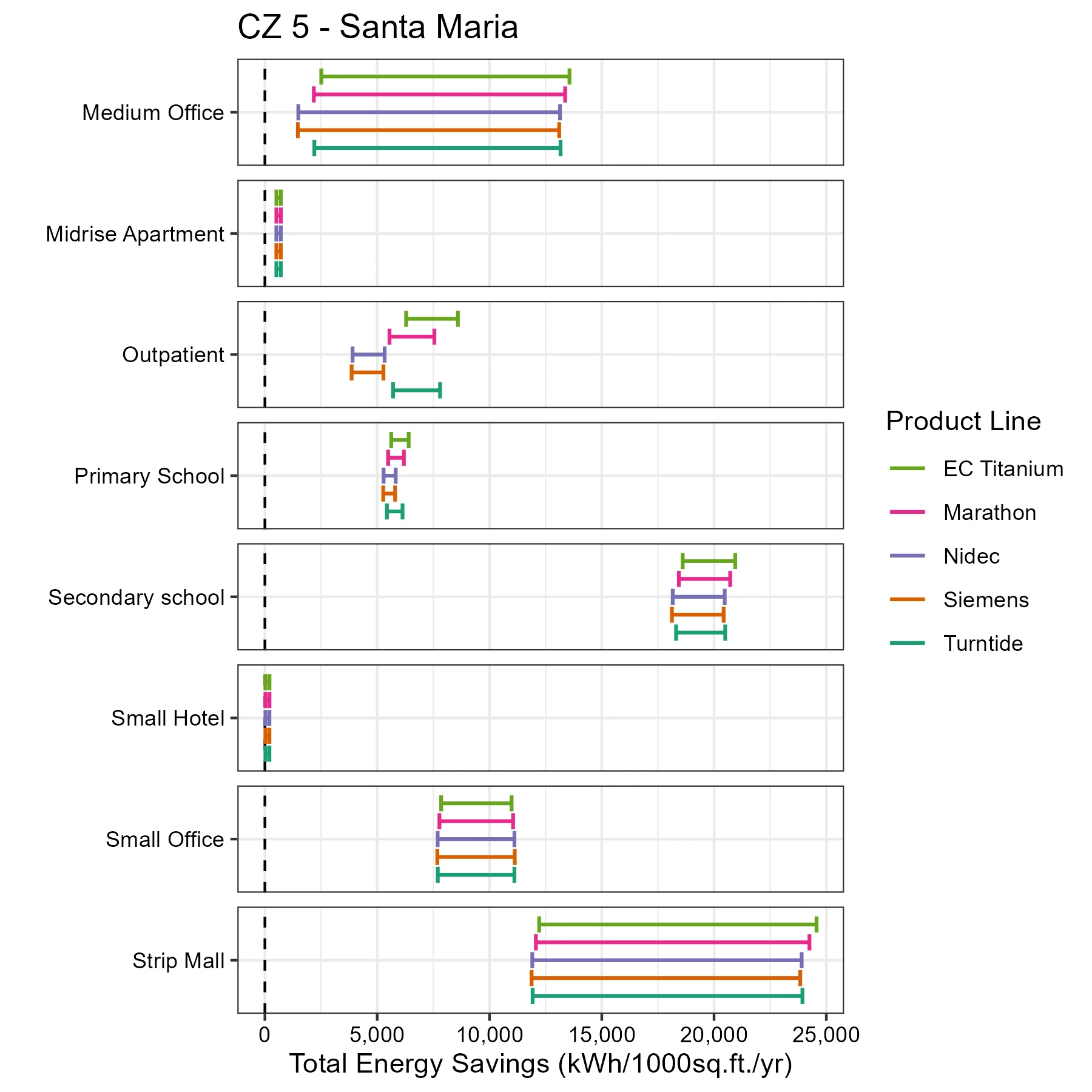
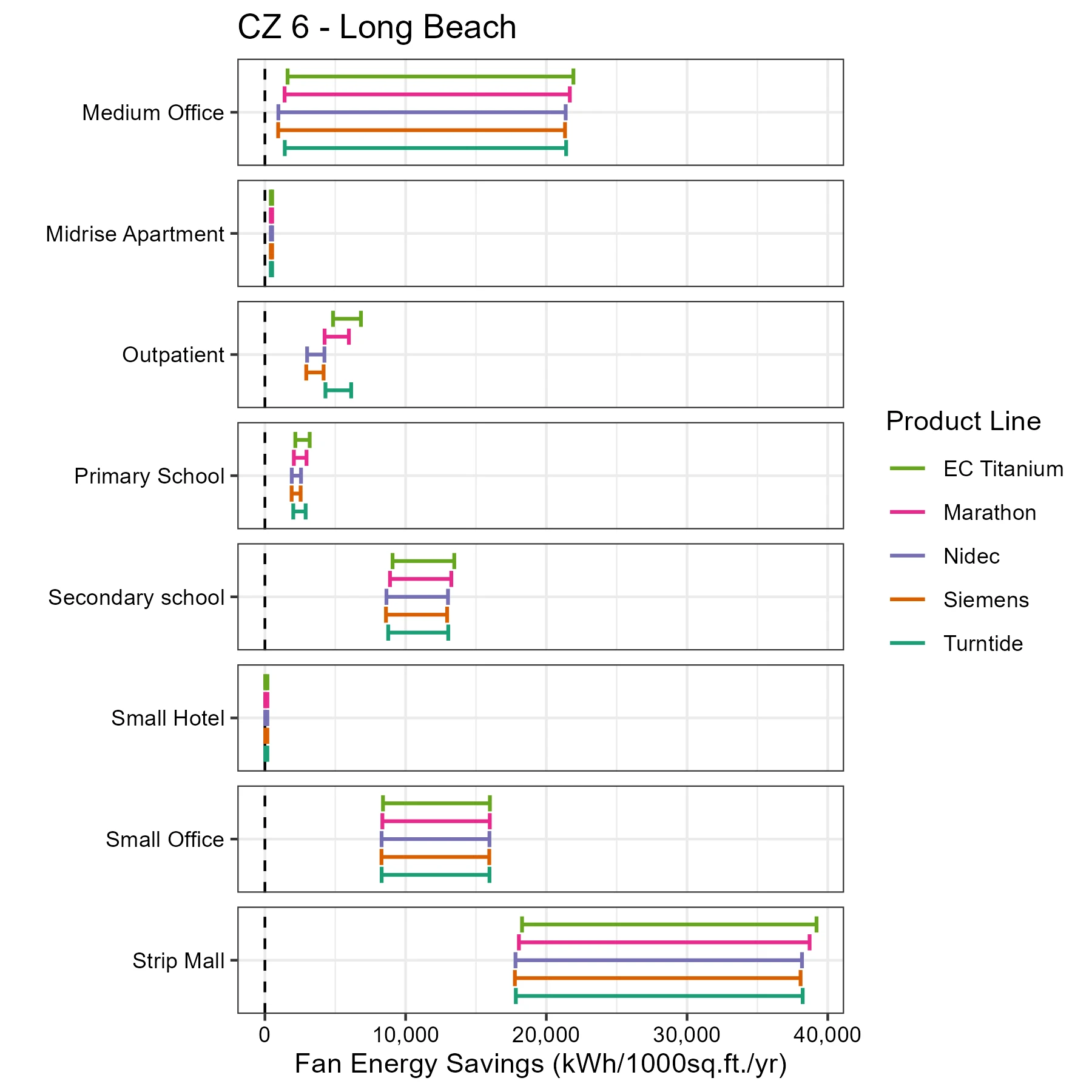
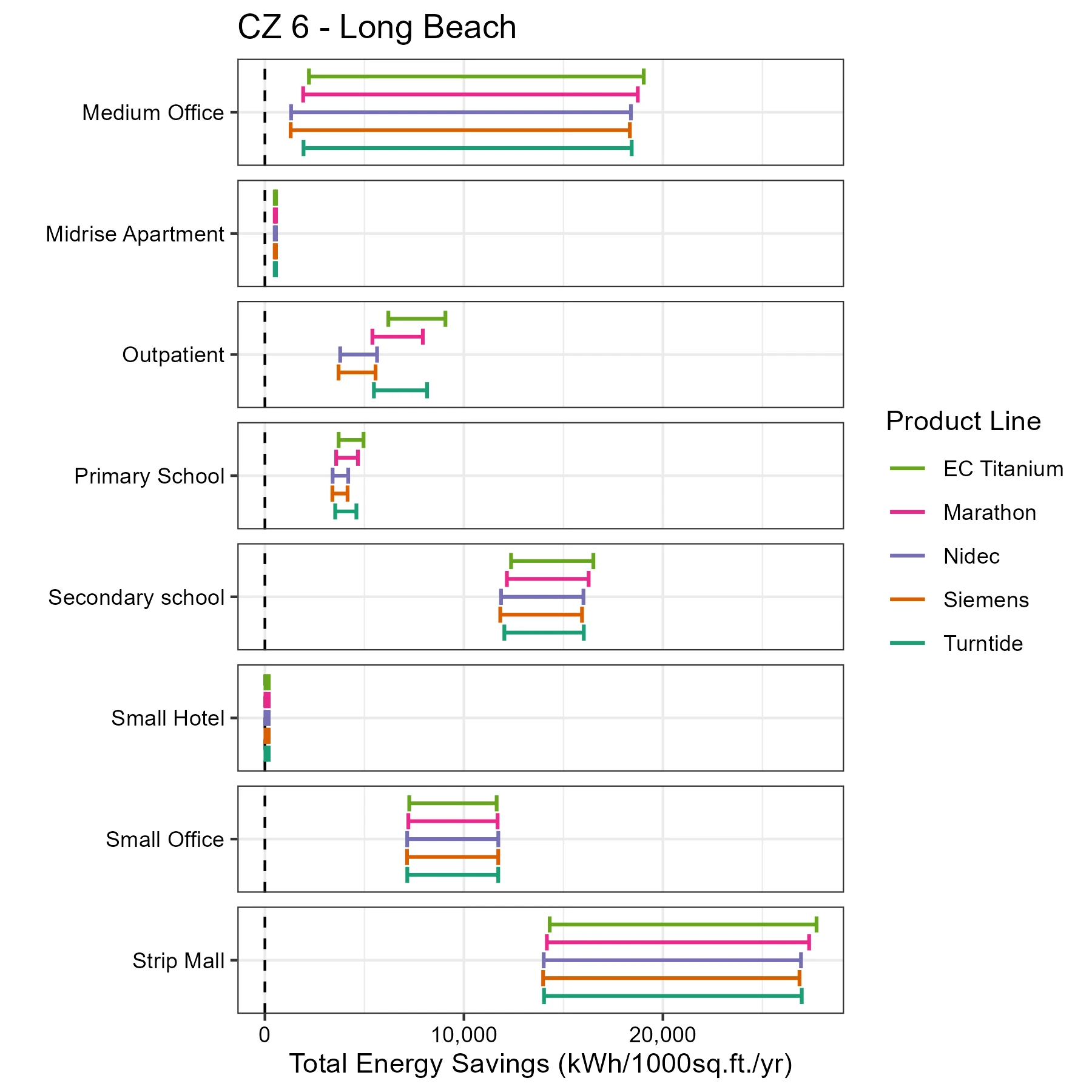
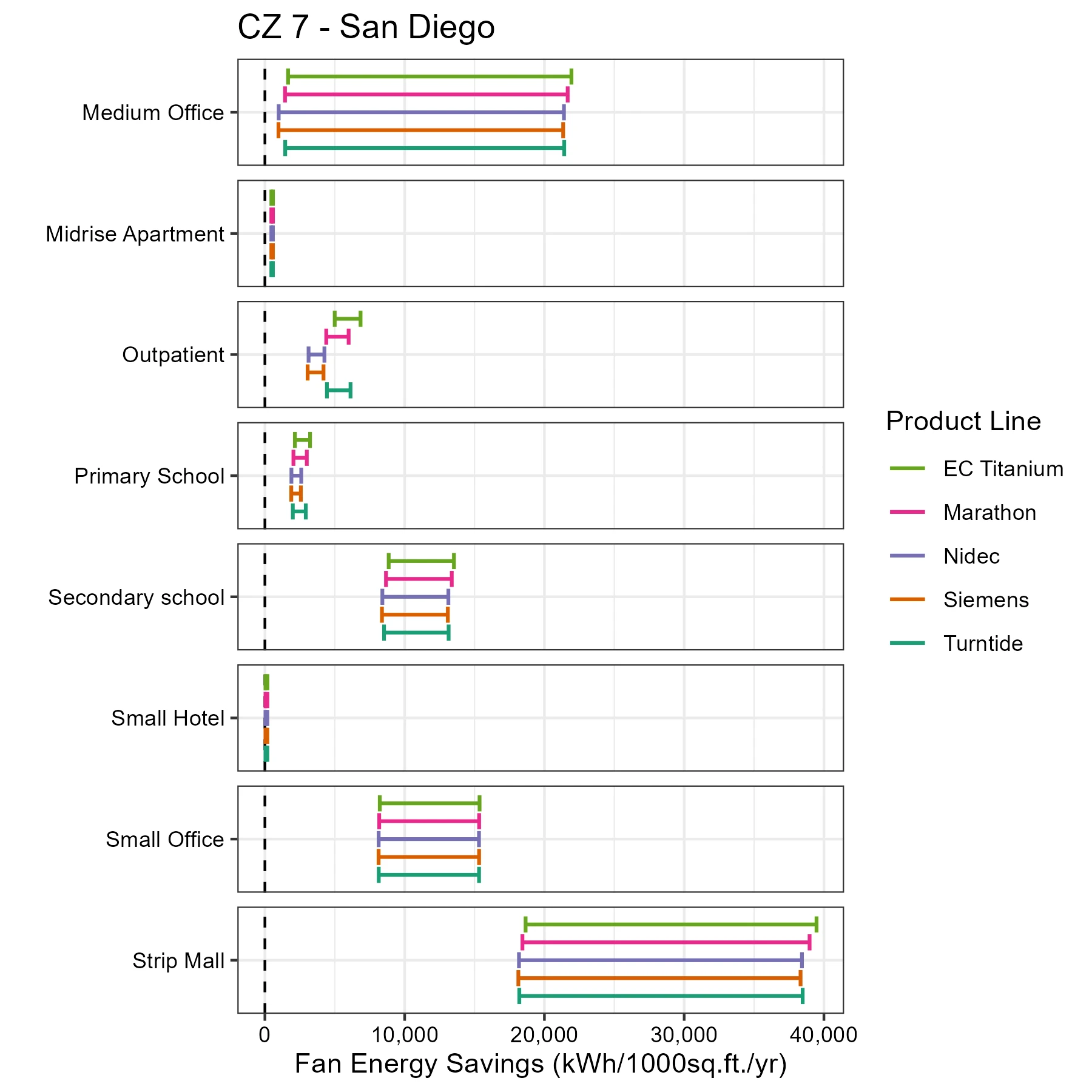
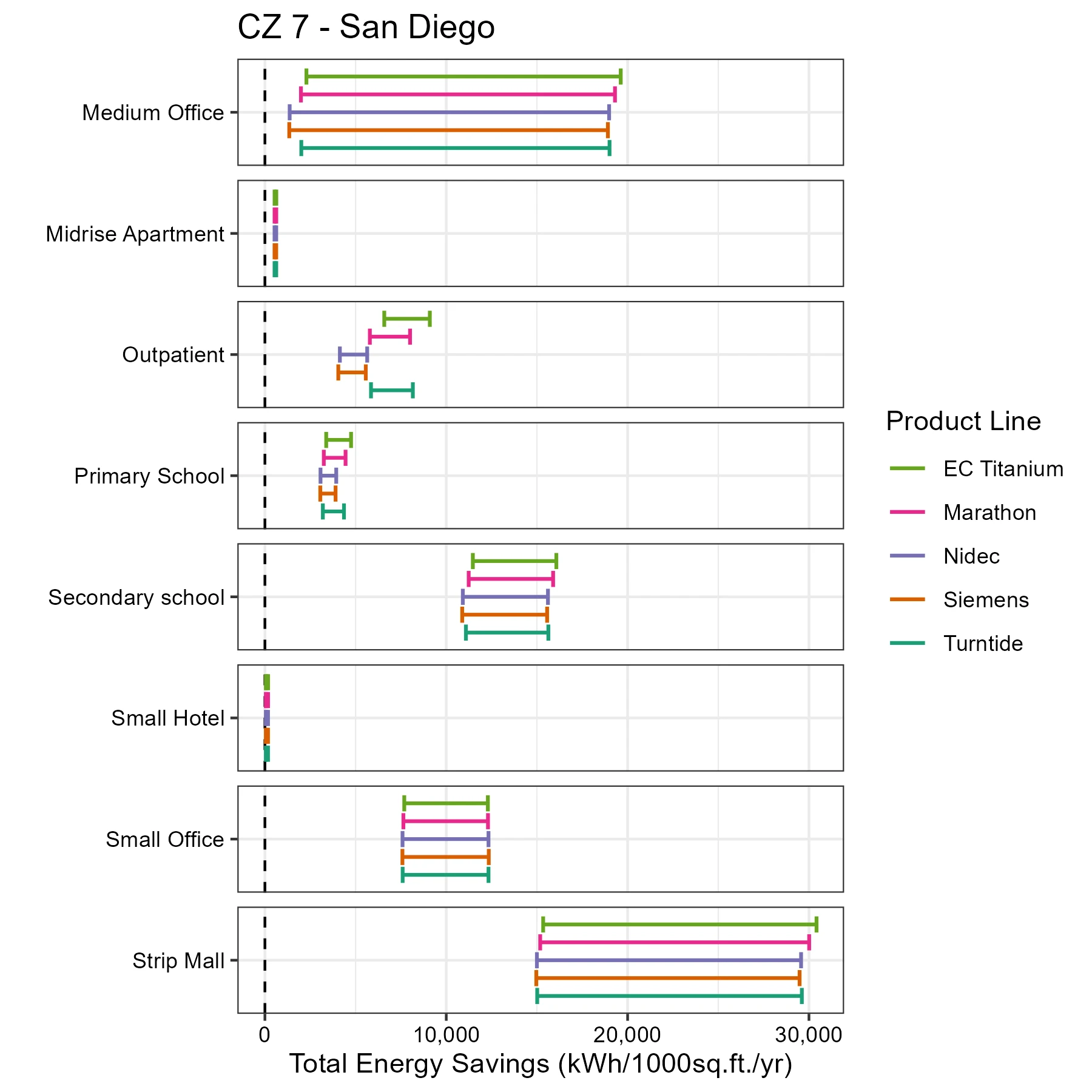
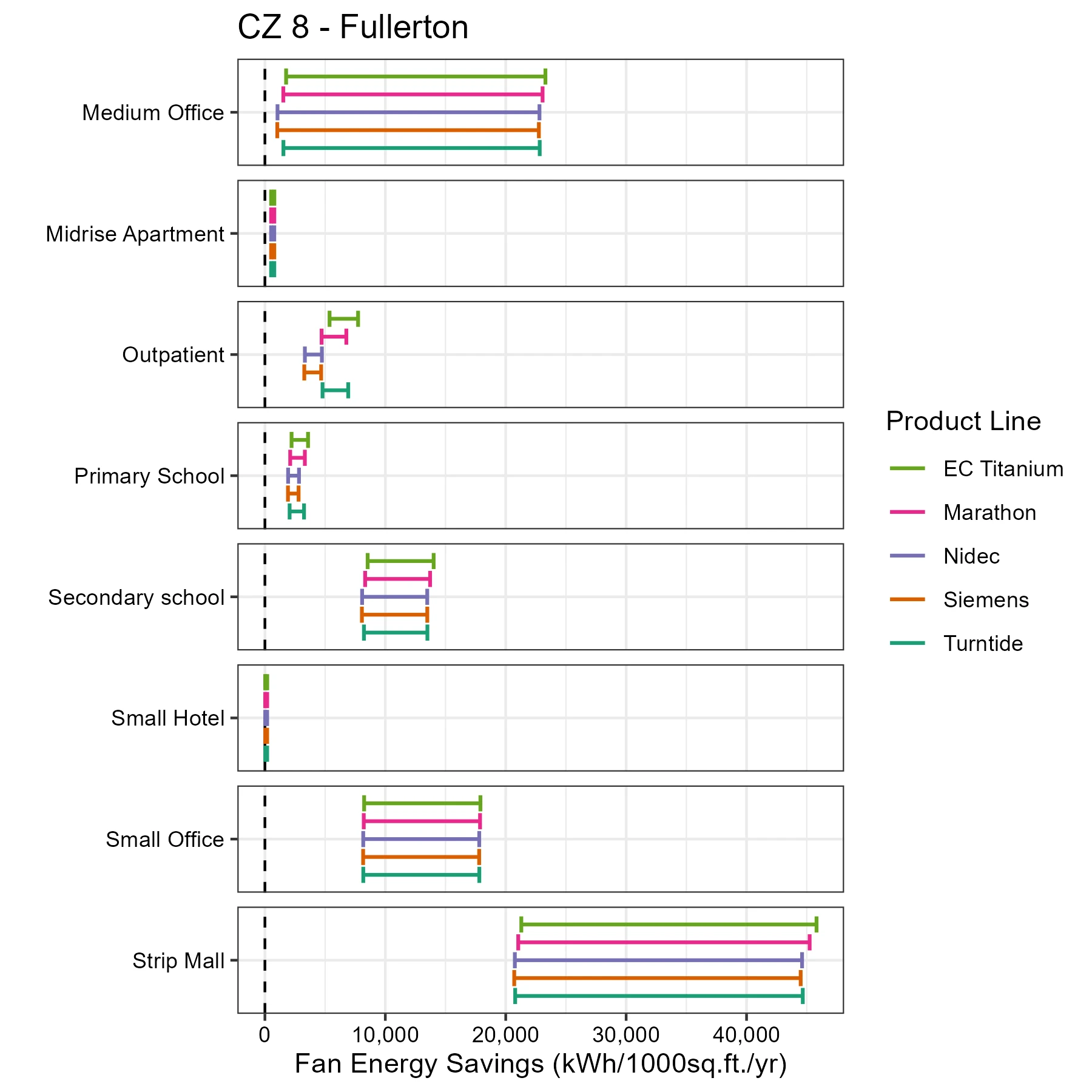
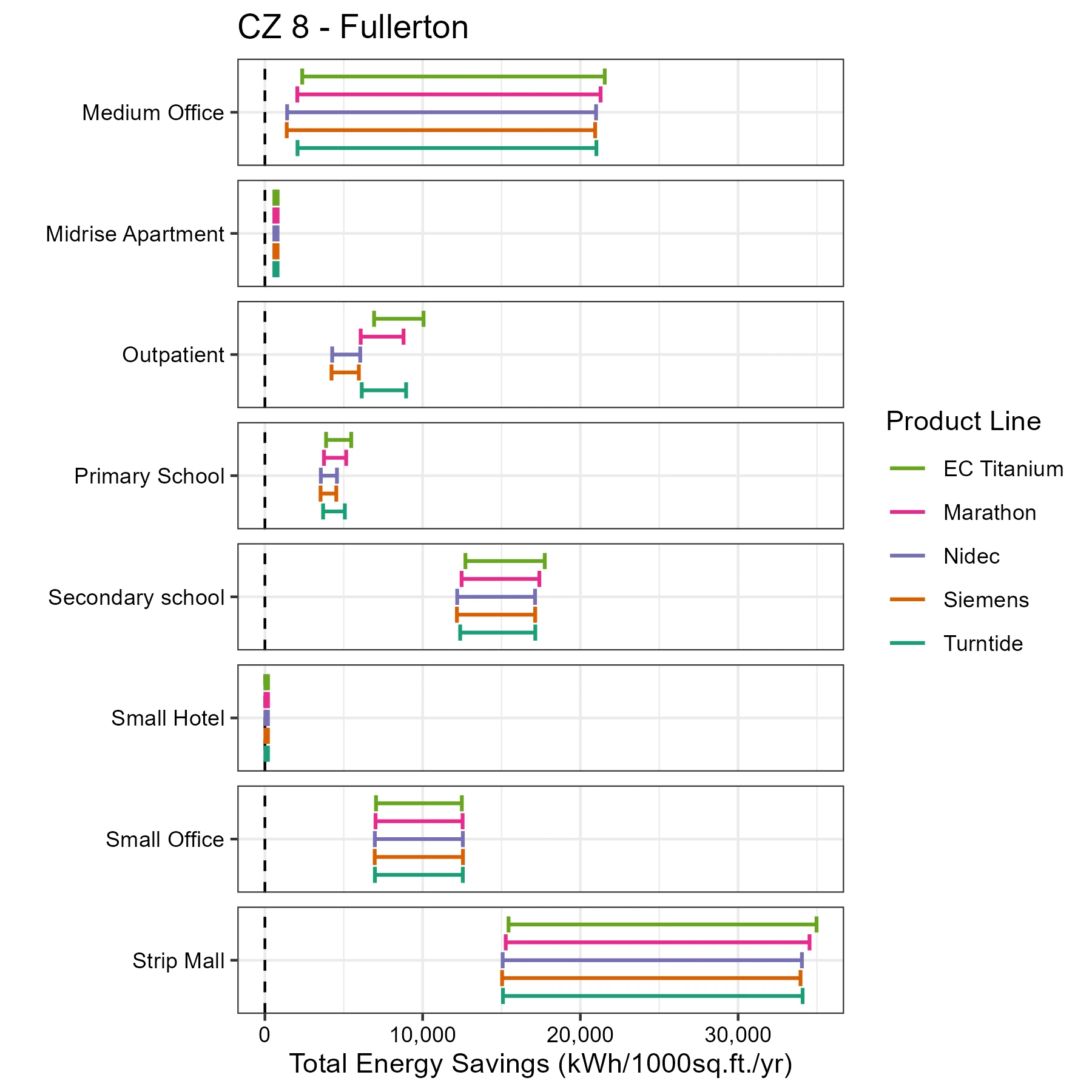
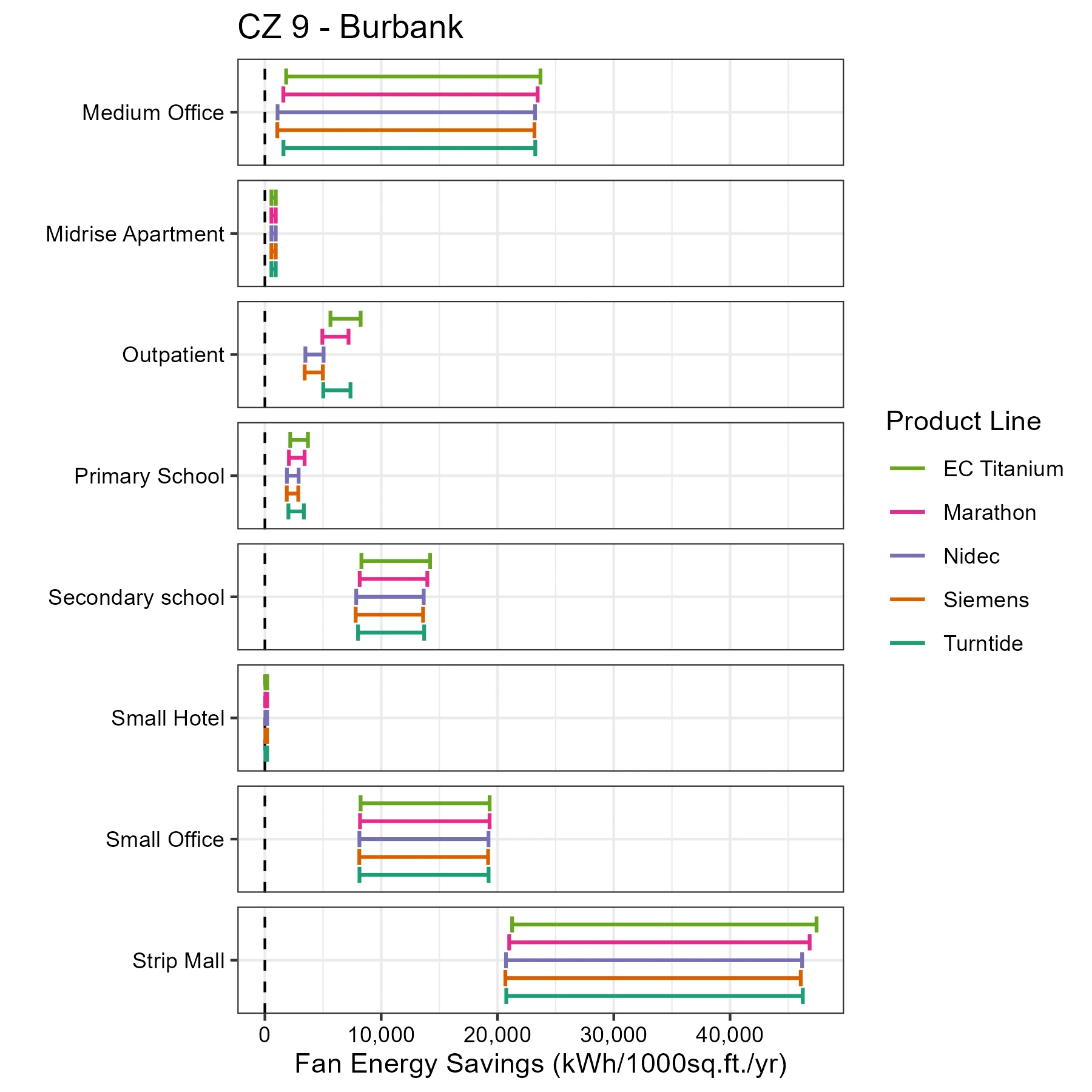
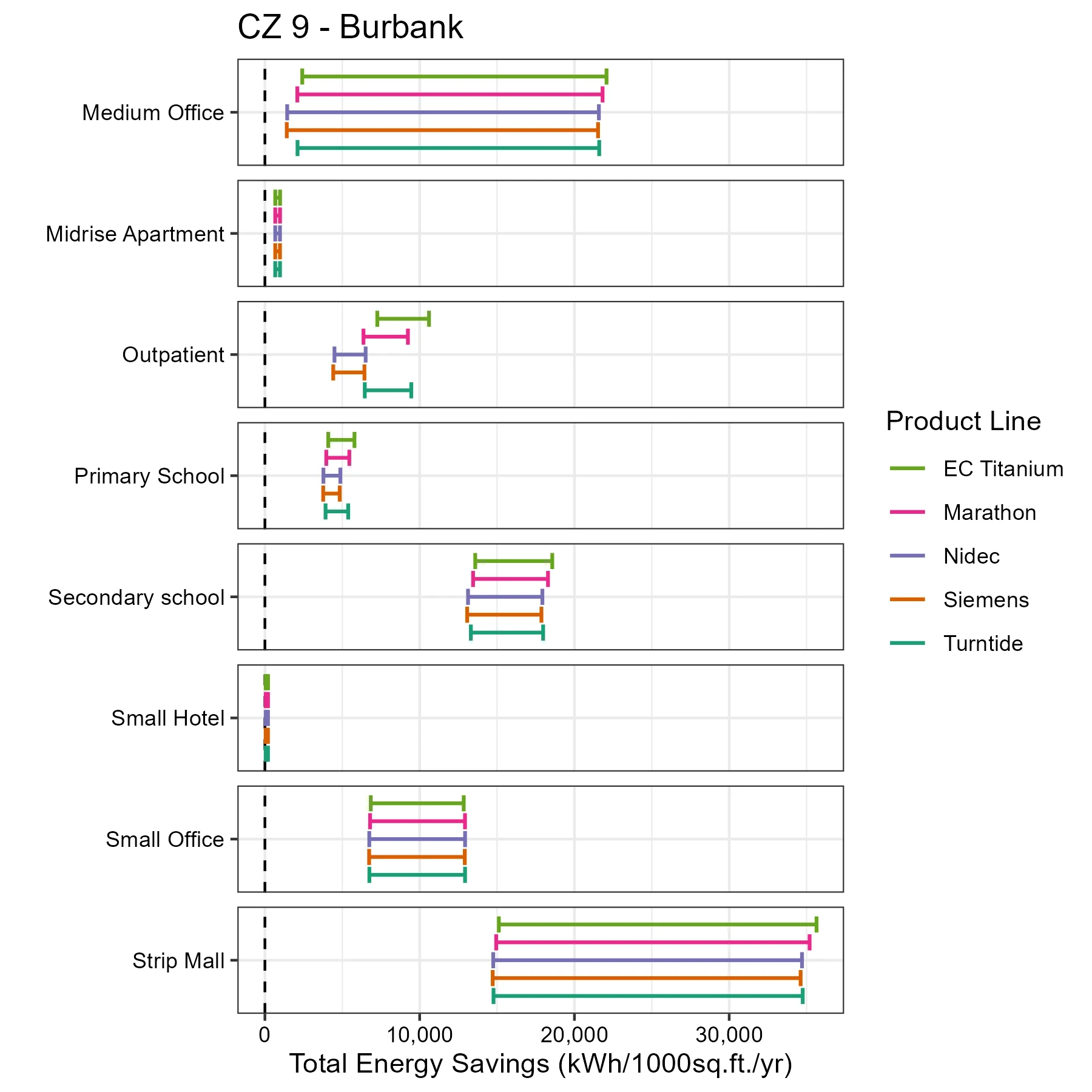
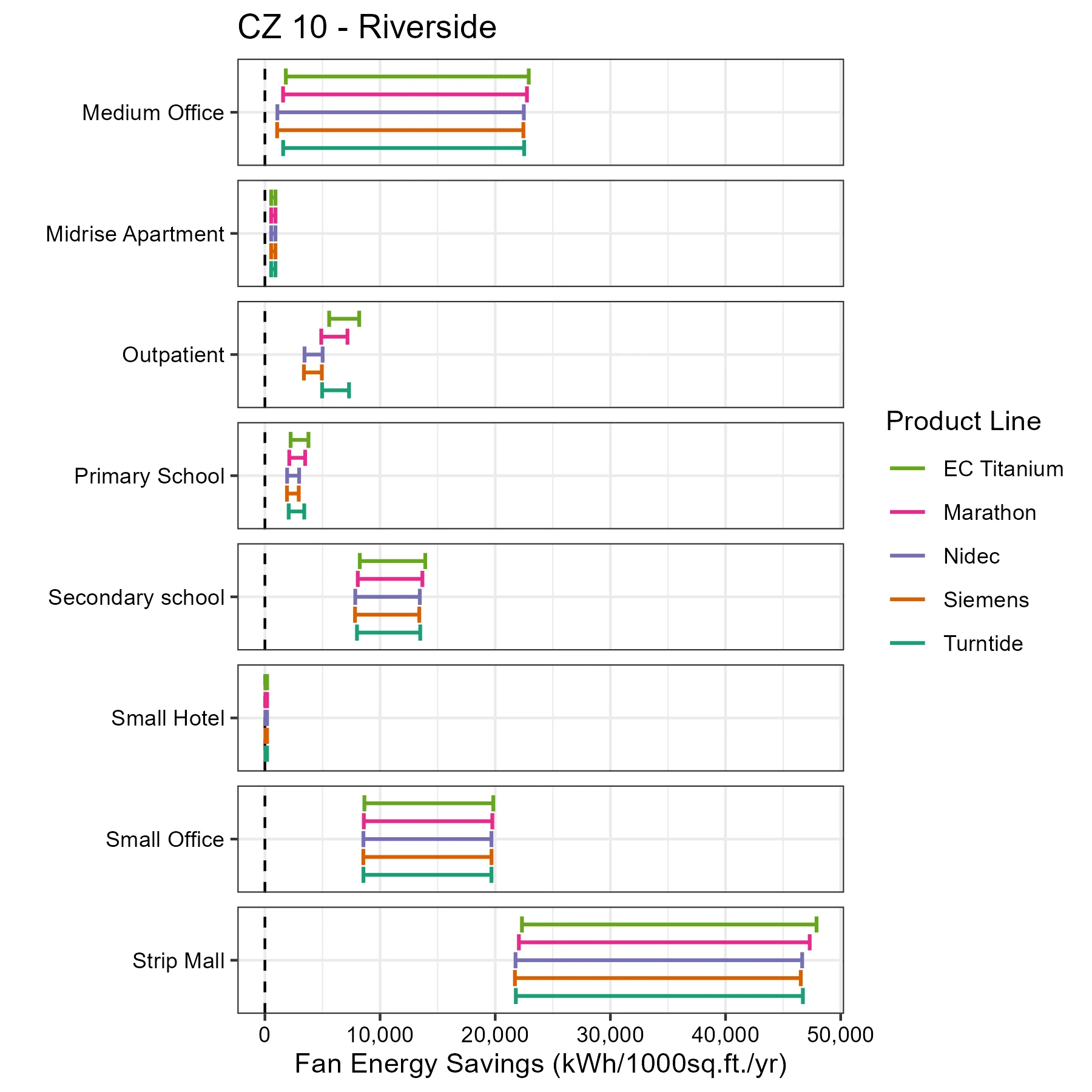
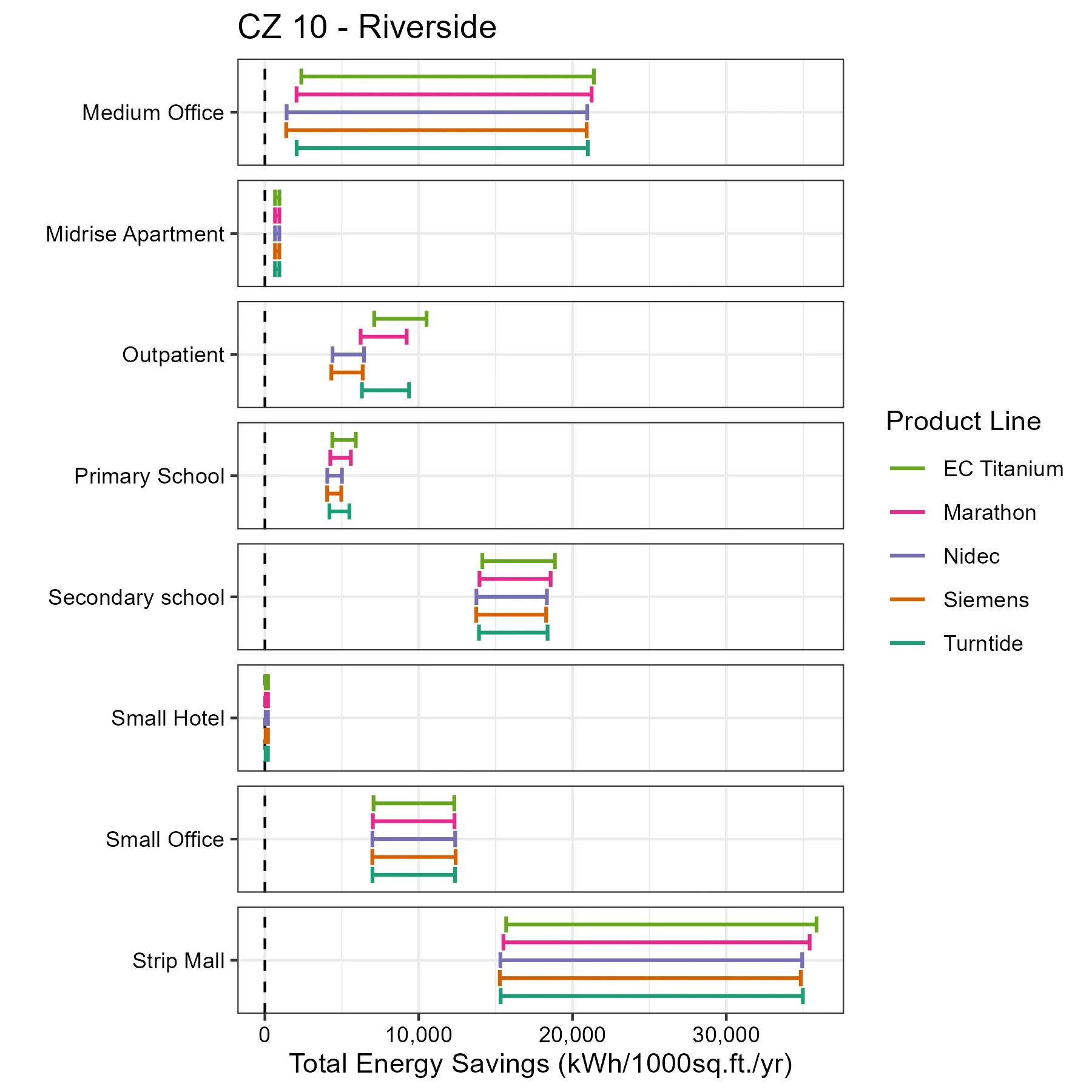
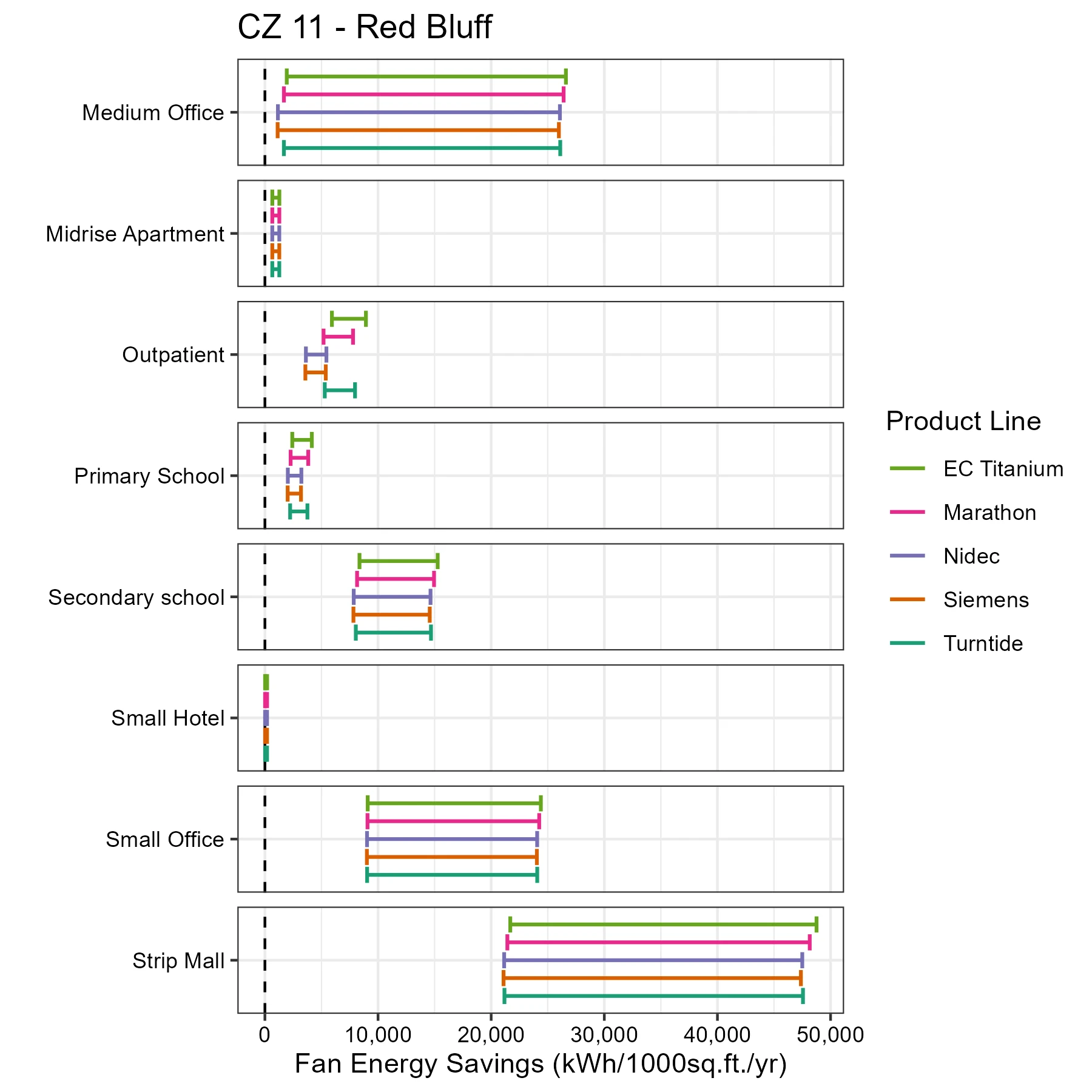
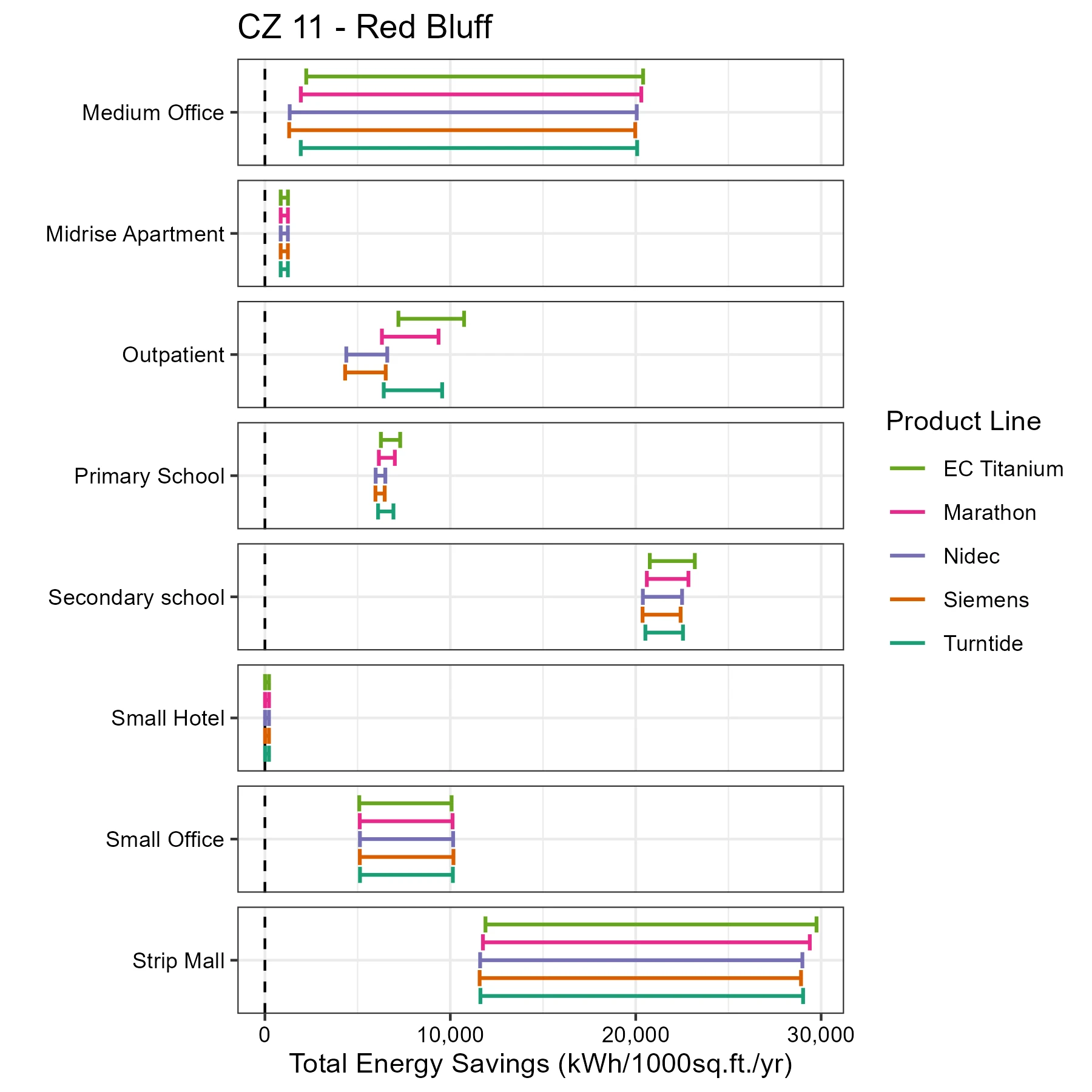
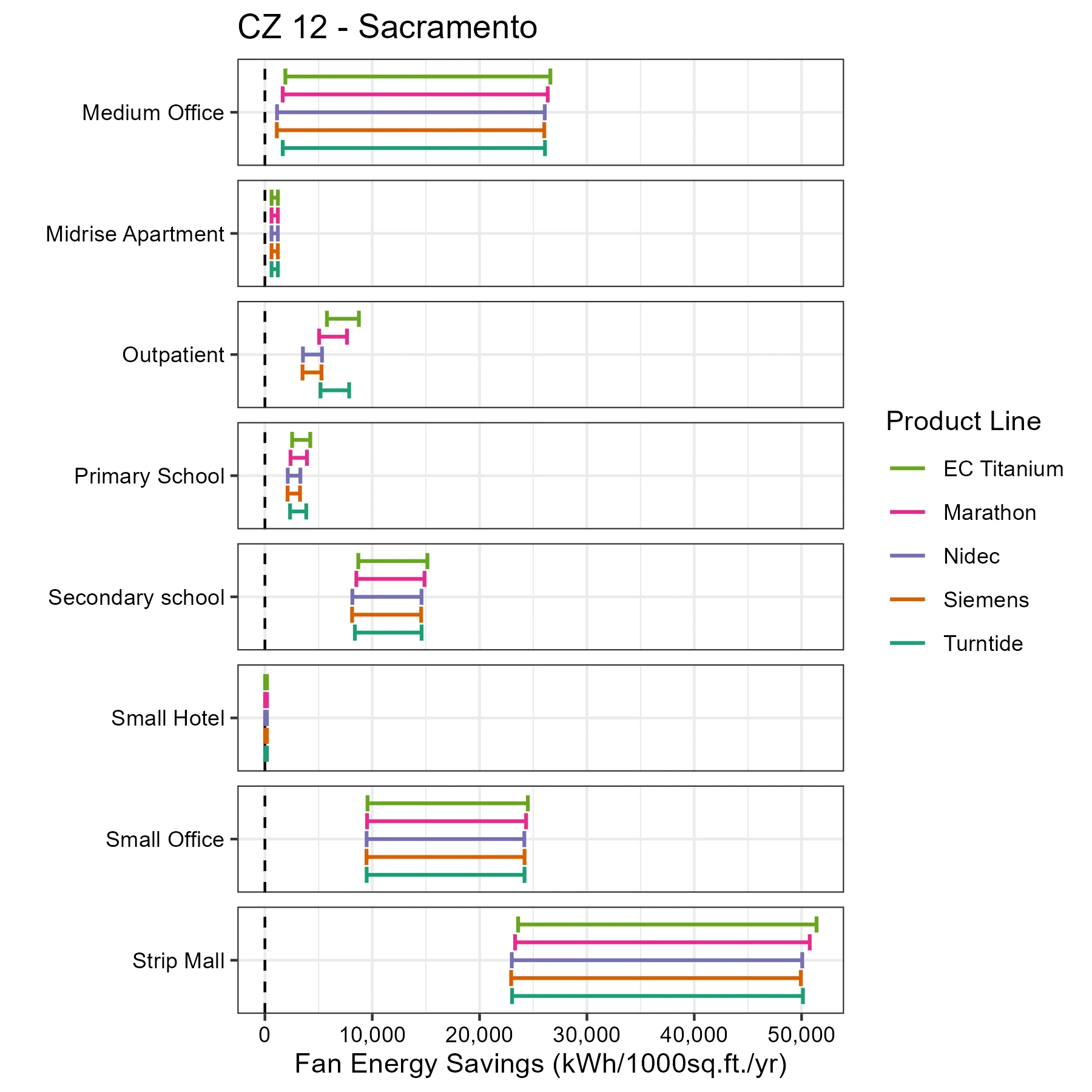
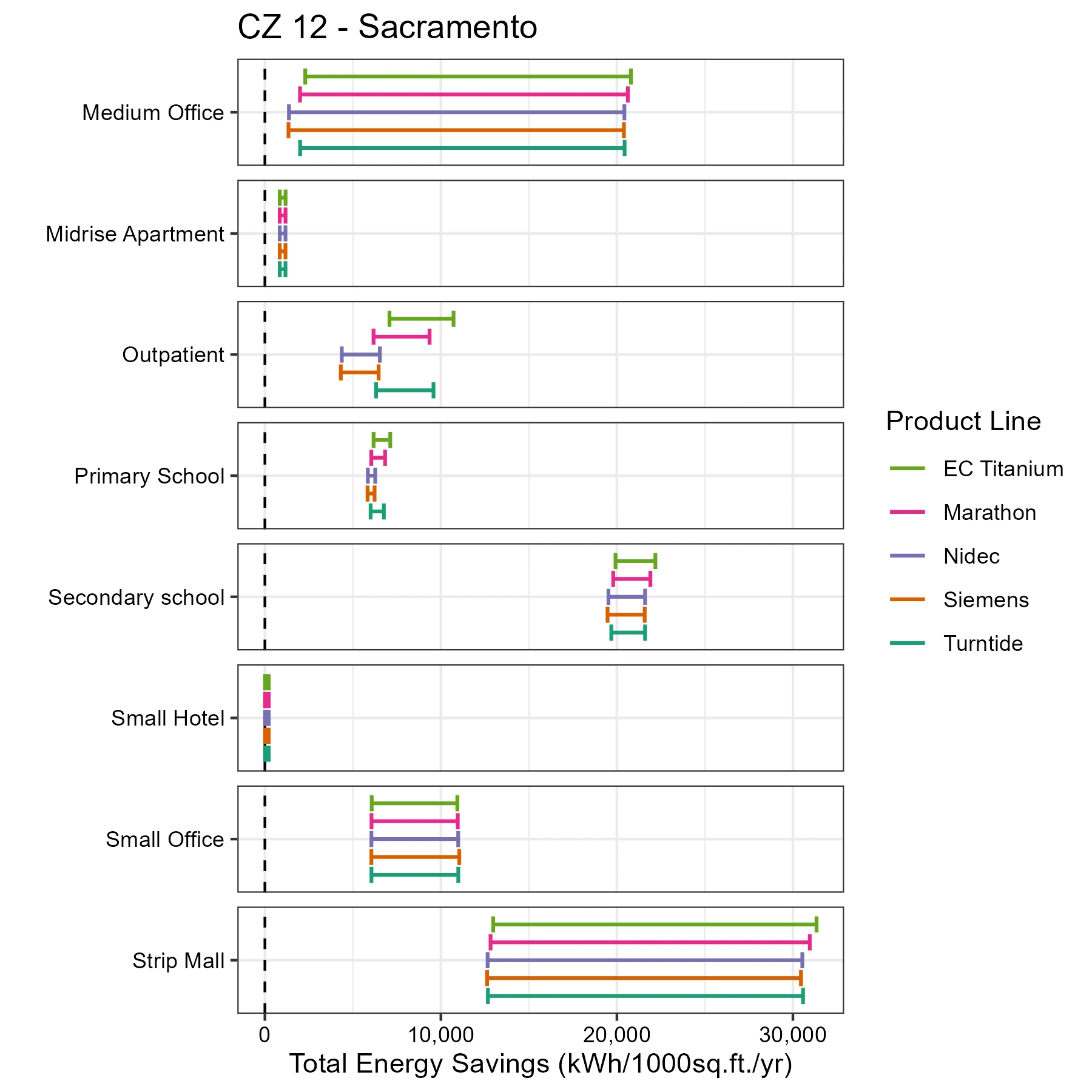
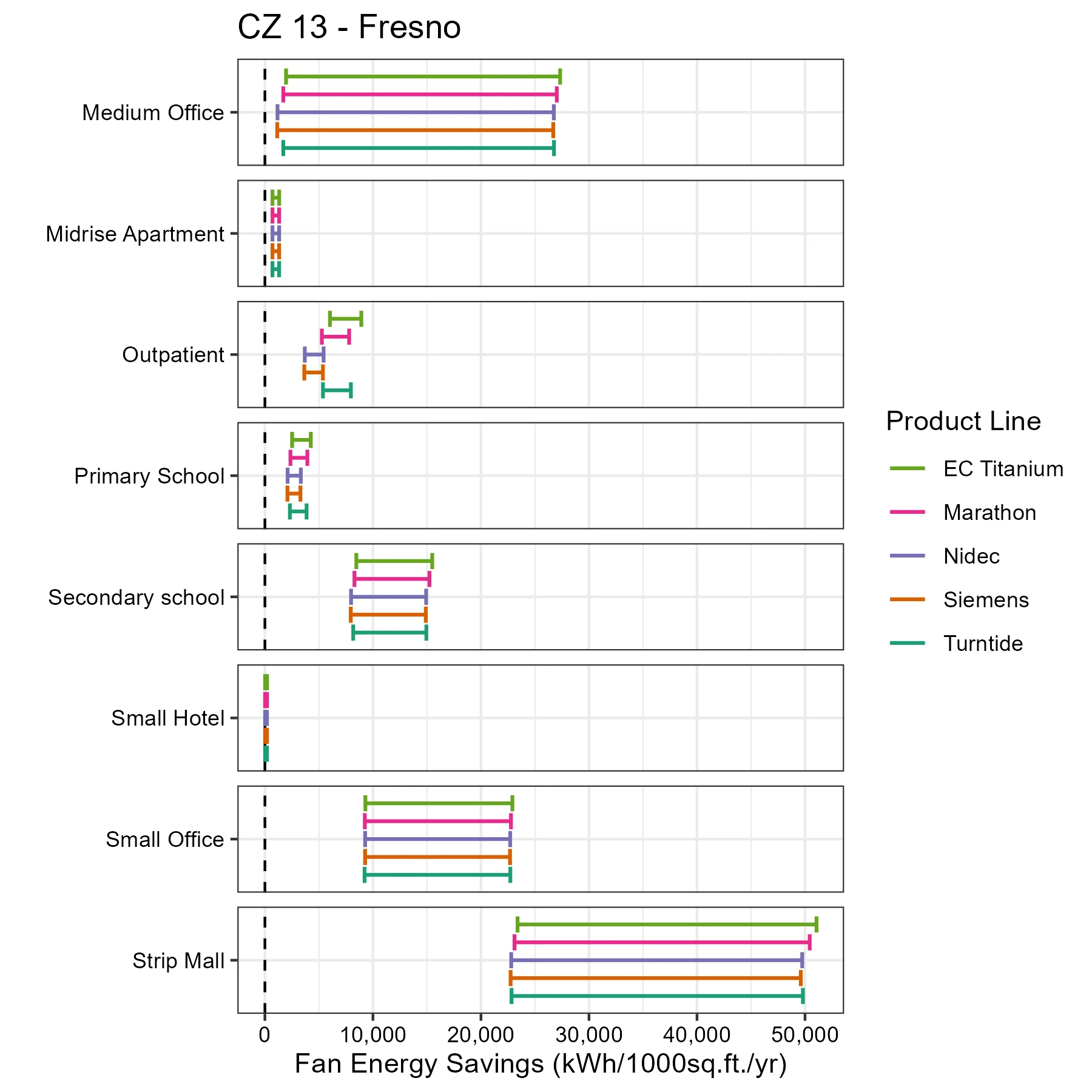
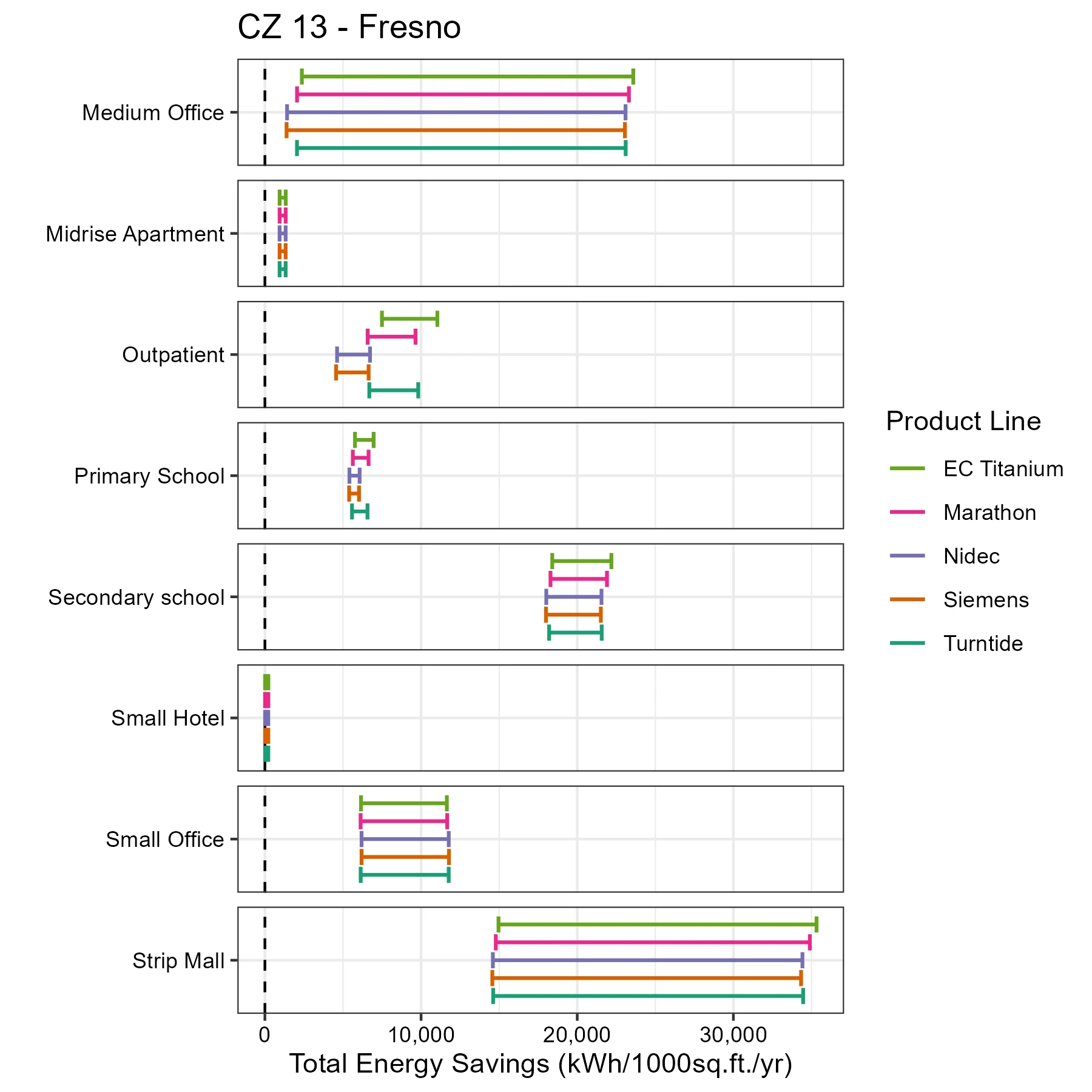
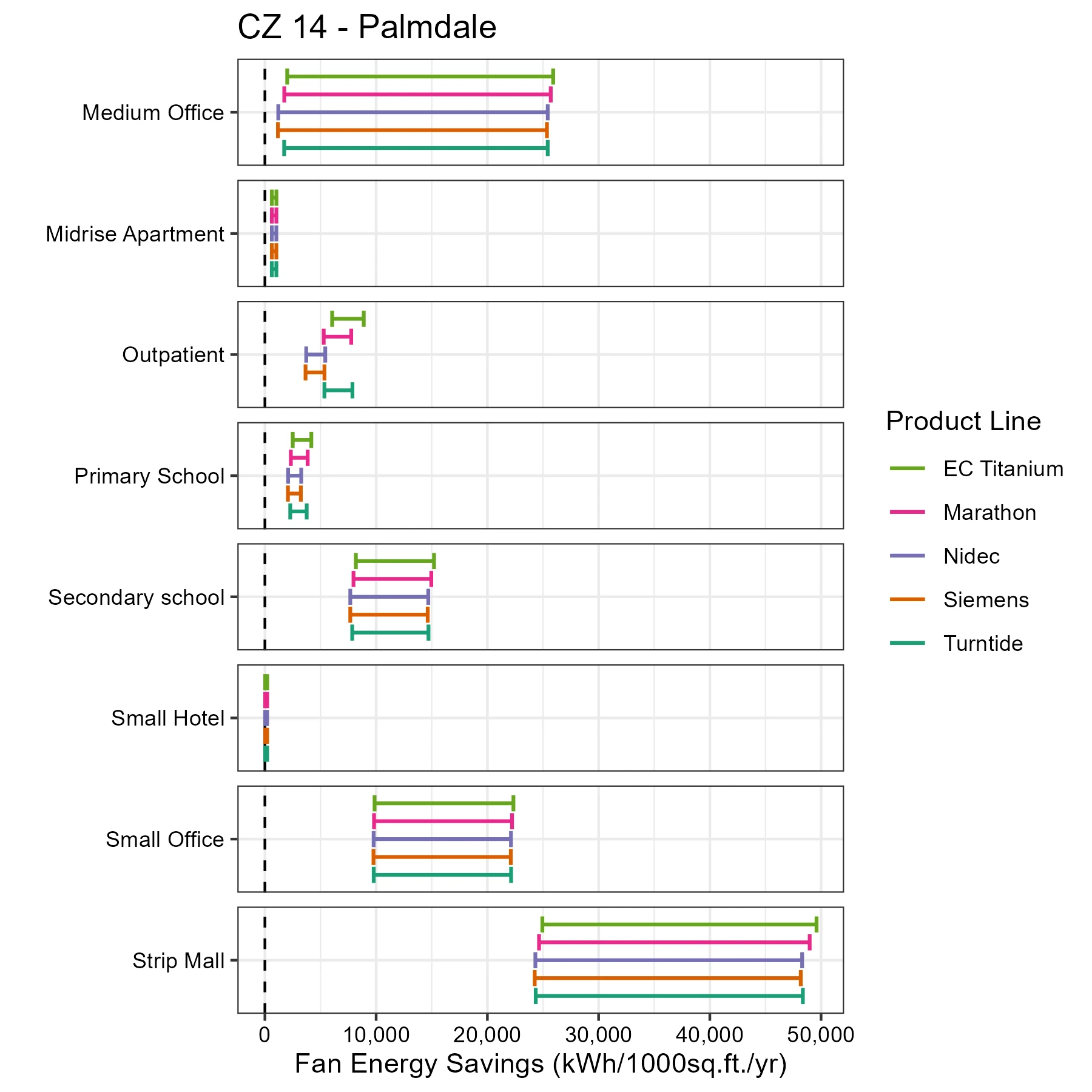
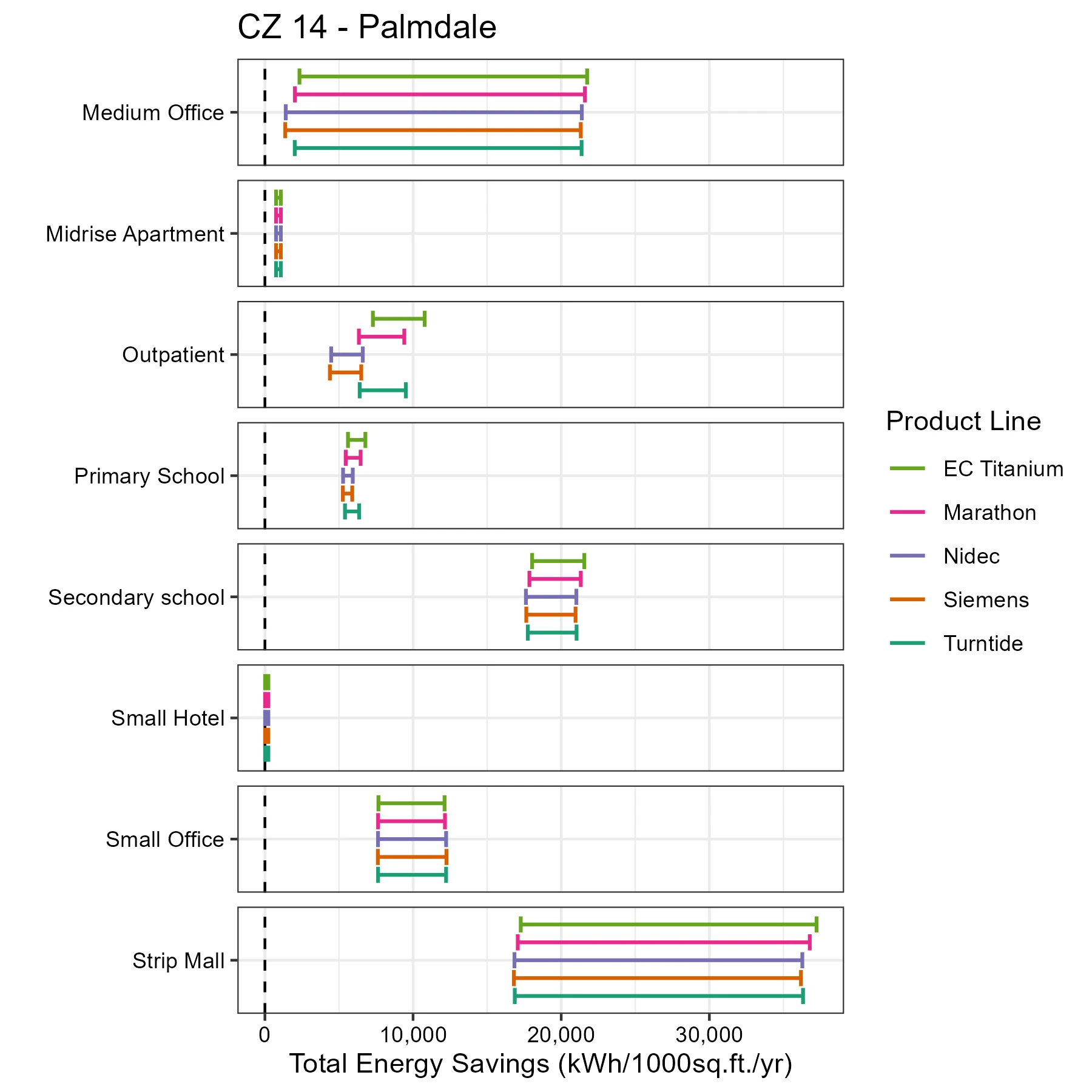
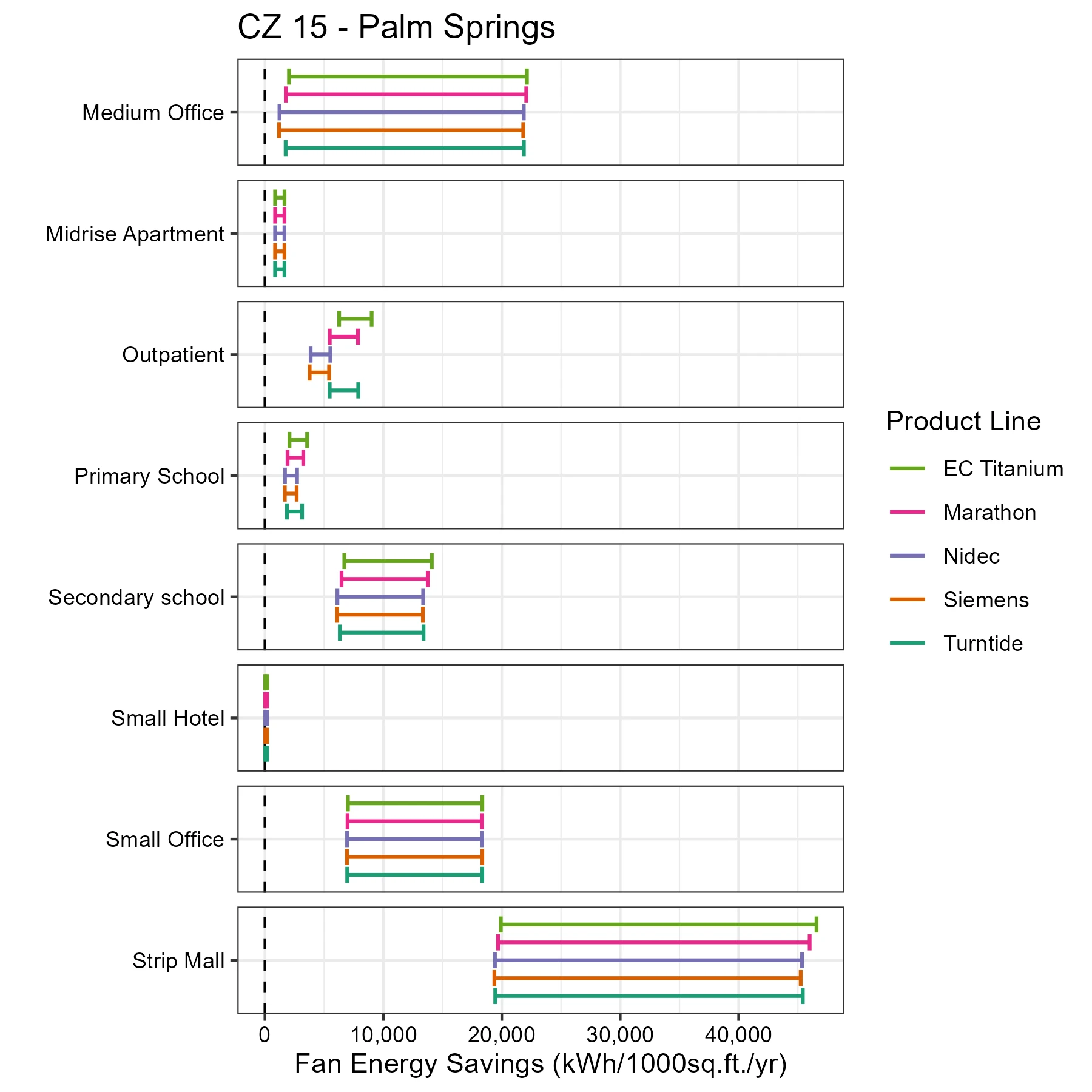
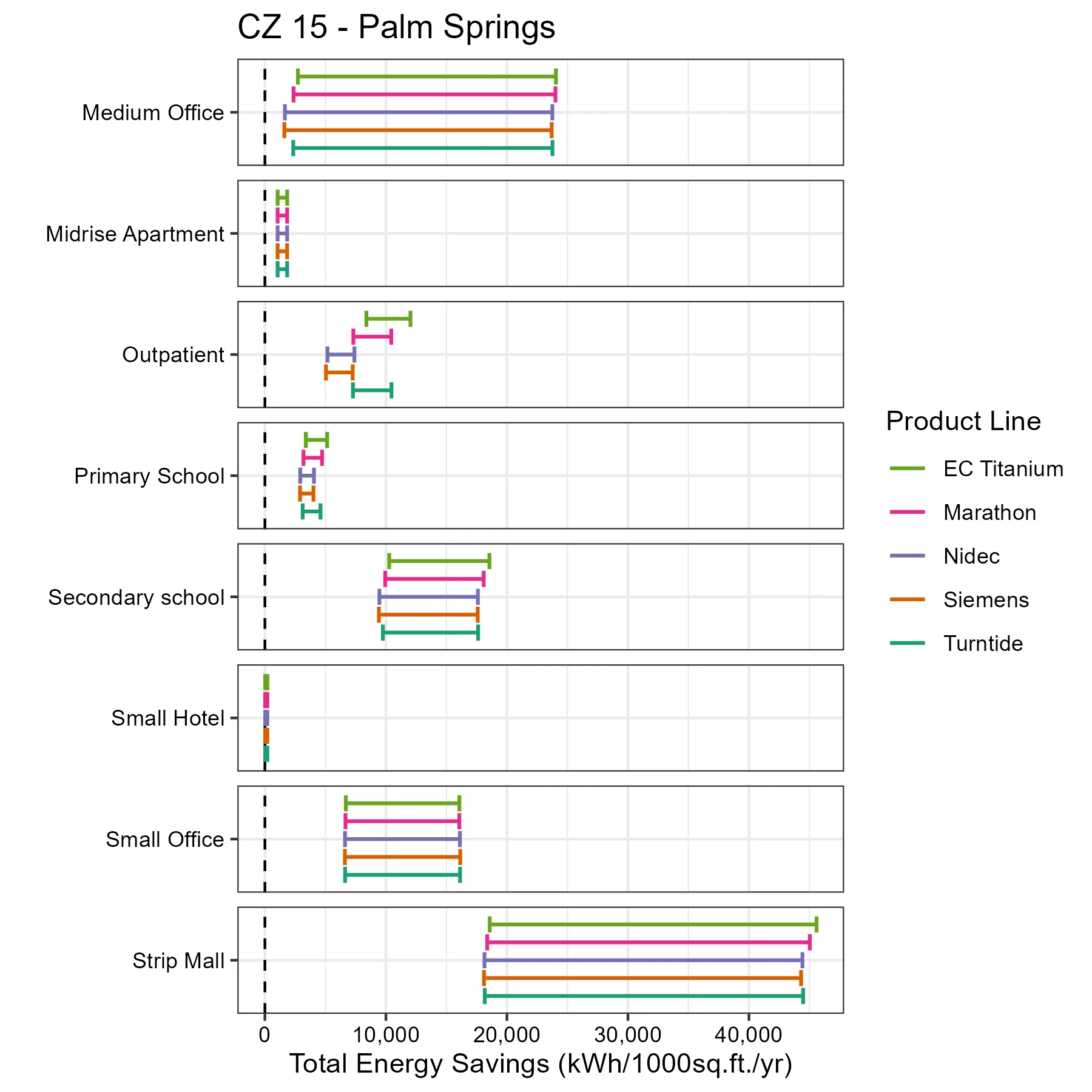
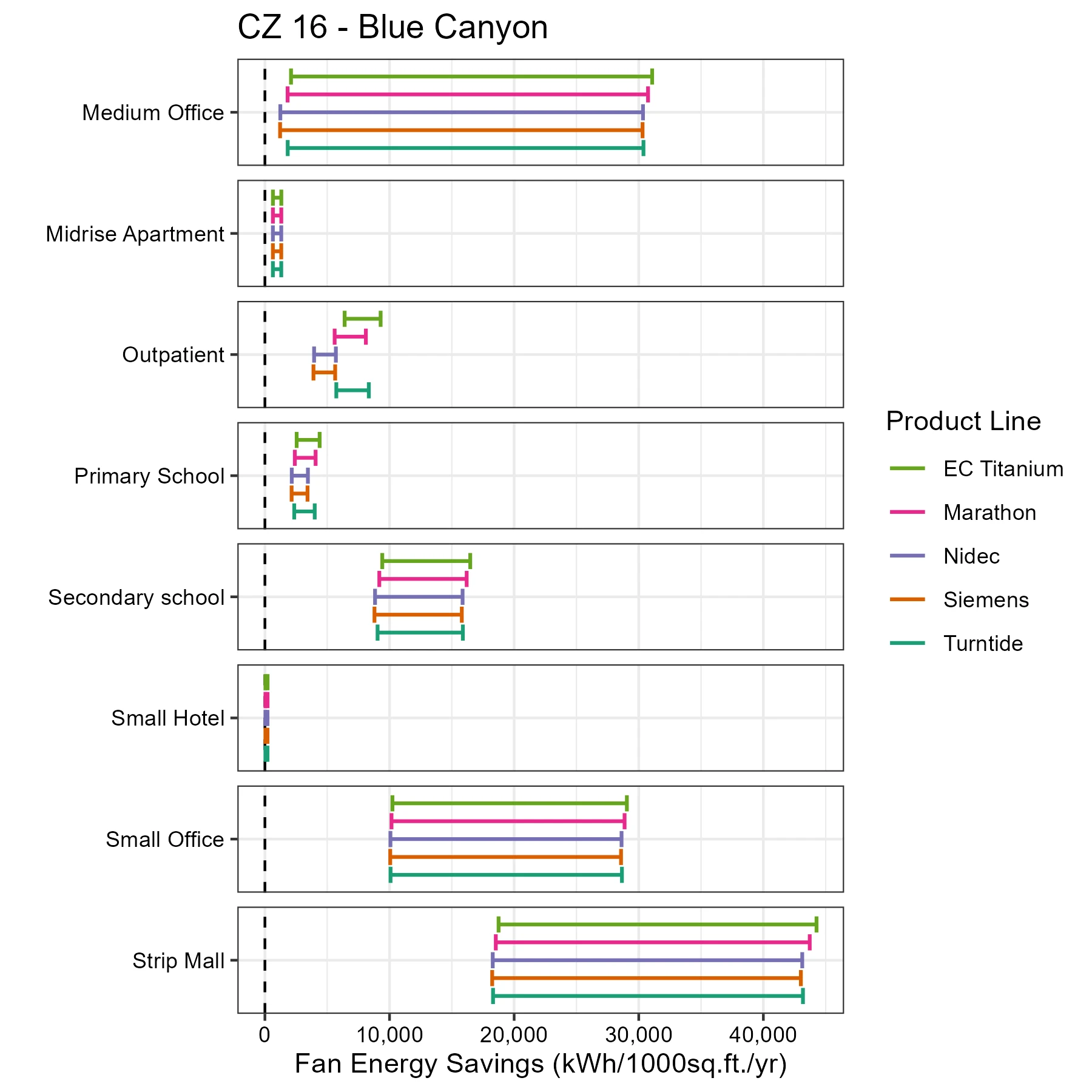
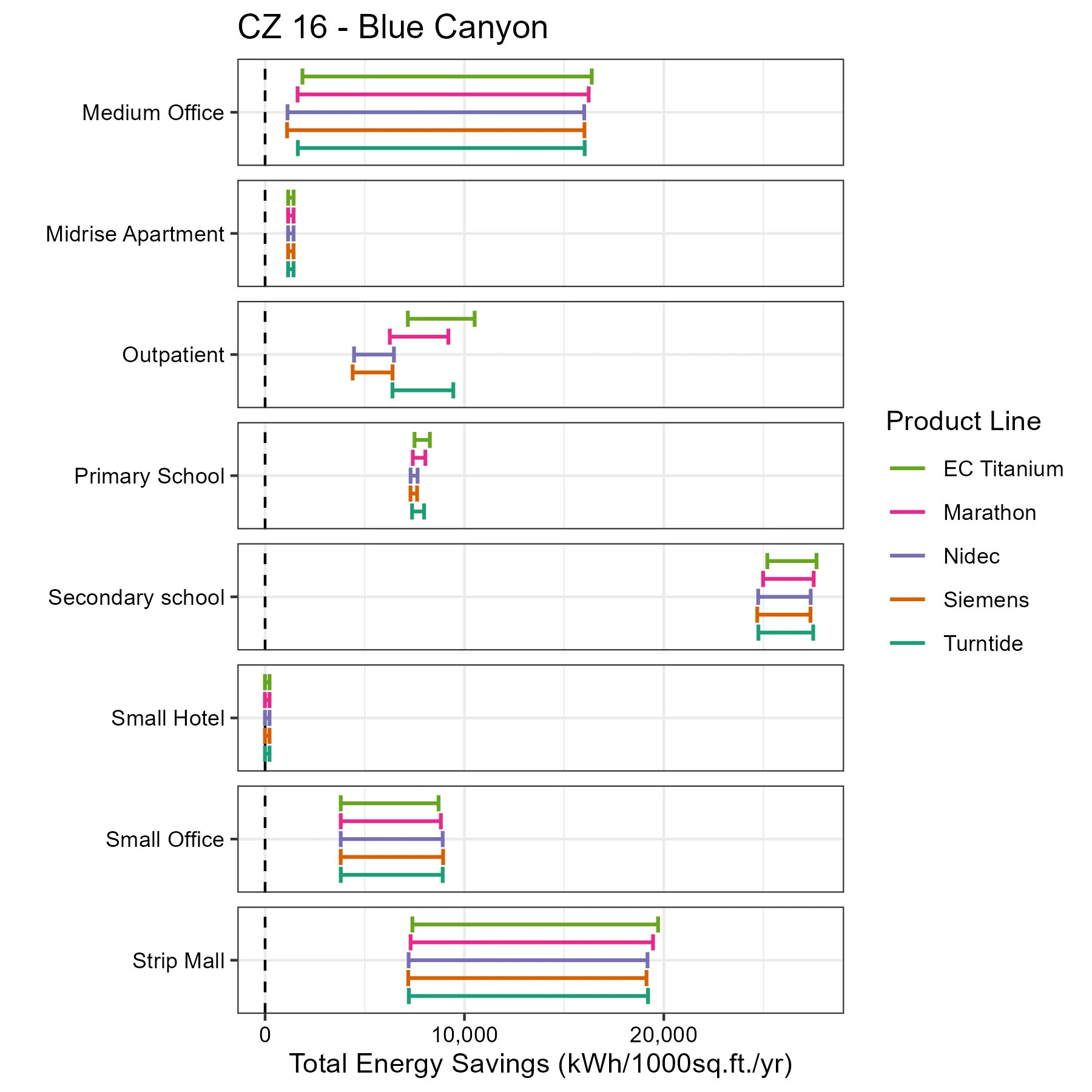